Use Value Engineering to Maximize Function and Lower Costs
This strategy can counter material shortages, without losing quality
An architect or a contractor is looking for a specific material for a project and learns that it’s not in stock, the lead times are too long, or the price is far beyond the project budget. Unfortunately, this is a common story for glazing contractors.
Material shortages can lead to an interruption of cash flow, affecting projects’ costs and timing. In 2021, supply chains were delayed by natural disasters and COVID. Construction material prices are projected to remain high and volatile throughout 2022.
Our industry is faced with a dilemma: How do we help our clients work around the financial constraints, maintain the functional and aesthetic goals, and ensure that the building is completed on time? The answer is value engineering.
Value engineering can maximize functionality and lower cost
Value engineering is not simply cost cutting, it’s about maximizing functionality at the lowest possible cost. It’s about not overpaying for product quality when equally effective options exist. It’s about looking for opportunities to cut items that don’t add value.
Thermally efficient proprietary cladding attachment solutions often are on the cutting list. Typically, its replacement is the continuous z-girt.
Substituting one cladding attachment solution for a cost-effective alternative that meets the requirements of the project is not necessarily a bad thing. But, the alternative solution should be equivalent in thermal efficiency, installation efficiency and material cost effectiveness. While continuous framing systems do not perform nearly as well as thermally efficient cladding attachments, they are still used.
Continuous framing systems are typically 18- to 20-gauge Z-girt or C-channel profiles attached vertically to the back-up wall. Cladding systems attach directly to the outer flange. With girt systems, the exterior insulation’s performance can be degraded significantly, up to 50 percent, depending on the configuration. Adding thermal breaks at the sheathing level can improve the thermal efficiency, but the insulation is still bridged.
The improvement largely affects surface temperature, rather than U-value. In terms of prescriptive code compliance, it is very difficult to meet effective R-value requirements with this system.
Use thermal modelling to confirm systems’ performance
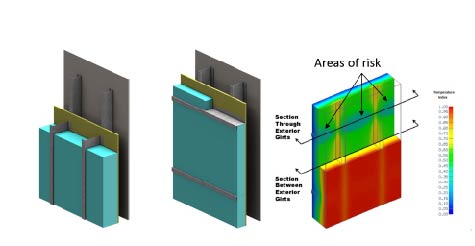
While substituting a girt system for a proprietary system might seem to solve a short-term cost problem, it also can introduce a long-term issue with condensation in the walls. Whenever a large, thermally inefficient building component’s surface temperature drops below the dew point of the surrounding air in the wall, condensation happens.
Over time, water in the wall can corrode metal, rot wood, crack masonry and degrade the cavity insulation. These conditions can lead to mold, mildew and other microorganisms, negatively affecting indoor air quality and occupants’ health.
Thermal modelling allows you to evaluate the wall system’s thermal efficiency, ensuring the attachment solution meets the specified U-value. It’s always important to validate performance before approving substitution requests. This critical step will ensure actual thermal efficiency is achieved for the building.
In addition to confirming performance requirements are met, thermal modeling allows you to further document that the substitution contributes to the architect’s design intentions, to the contractor’s budget and schedule, and to the overall value engineering goals.