Architect’s Guide to the Glass Recycling Supply Chain
Creating opportunities for greater glass recycling and circularity
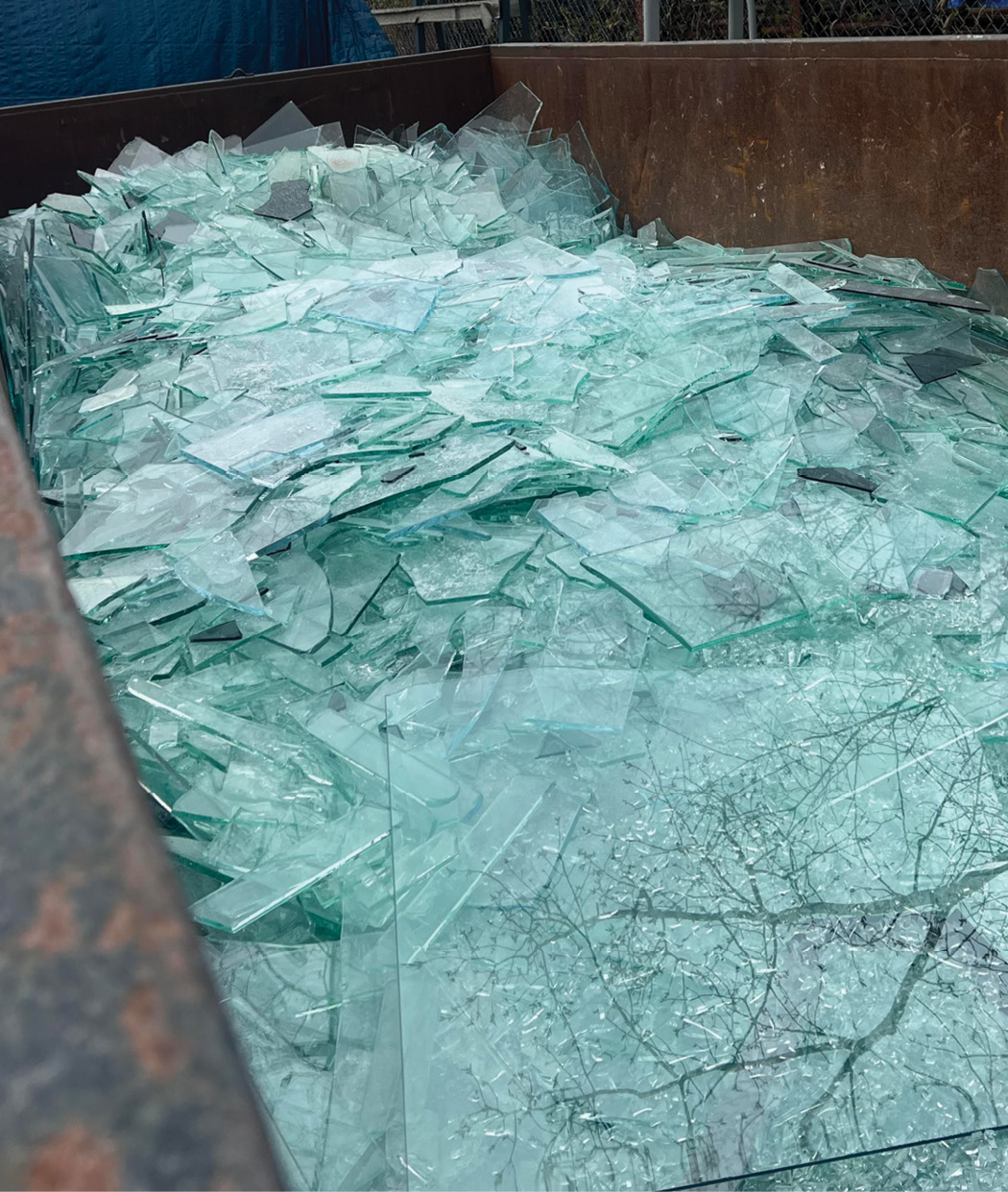
Above: Large container with broken flat glass pieces destined for recycling. Photo courtesy of Resource Recovery.
Glass is being asked to do more in terms of performance, aesthetics, and now, reducing the cost of carbon on our environment. Both glass recycling and circular building design can aid in these efforts.
“Glass is a super material,” explains Sophie Pennetier, founder of Digne, an academic-industry work collaborative. “It’s super inert, it’s super transparent, it’s as strong as steel in compression, and it’s as elastic as aluminum. It’s a very versatile material.” Additionally, glass has important sustainability attributes. It is infinitely recyclable. And it can be adapted and reused in building applications.
Buildings generate nearly 40% of global carbon dioxide emissions, according to Architecture 2030. The embodied carbon of building materials, referring to the CO₂ used to manufacture those materials, accounts for 11% of those emissions.
Recent legislation requires greater material transparency regarding the embodied carbon of products, including life cycle assessments and the creation of environmental product declarations, which account for the CO₂ emissions used to create building products. Despite greater regulatory interest in reducing embodied carbon, incentives for glass recycling and circularity remain complex in North American.
What are some uses for recycled glass?
- Glass containers such as jars and bottles
- Road grade
- Fiberglass
- Reflective highway paint
- Landscaping products
- Countertops
- Coastal restoration materials
- Carpet backing
The glass recycling supply chain
The float glass process recycles virtually all the glass waste, called cullet, from the in-plant production melting and cutting processes.
Pre-consumer cullet. Cullet generated within the same float glass plant can be reintroduced to the original process. Many float manufacturers also have agreements with glass fabricators to return glass cut-offs, created during the glass fabrication process, which can be used as part of the float manufacturing process.
Using glass cullet in the float production process reduces carbon emissions because fewer raw materials are being used, and the flat glass can be formed at a lower temperature. According to Glass for Europe, recycling 1,000 tons of cullet can result in a savings of approximately 600 tons of CO2 emissions, lowering the embodied carbon of the float glass.
Float manufacturers must ensure the quality of their cullet. Contaminants in recycled glass, such as aluminum, nickel, ceramics and other metals could compromise the float bath equipment and negatively impact the quality of new glass, leading to issues like downtime and potentially very expensive equipment maintenance if extreme care is not taken. While aluminum and nickel are two of the most concerning elements, all types of contamination can cause serious damage to a glass furnace and the glass products produced from an architectural float.
Pre-consumer cullet does not qualify as pre-consumer recycled content for green building initiatives such as LEED Building Product Disclosure and Optimization-Sourcing of Raw Materials credit.
Post-manufacturing glass waste. Float glass manufacturers typically do not recycle post-consumer or pre-consumer recycled cullet from glass fabricators or other sources primarily due to glass composition differences and possible contamination.
Glass fabricators should establish a working relationship with their nearest glass recycling company in order to lower freight costs and drive the highest value for this material. The National Glass Association recently launched a new glass recycling map to make this process easier.
Recyclers, sometimes called municipal/mixed/material recycling facilities or MRFs, typically accept glass from a broad spectrum of suppliers and industries beyond just glass fabricators, such as automotive, solar, appliance and electronics. Knowledge of how to leverage value across many different end markets is needed.
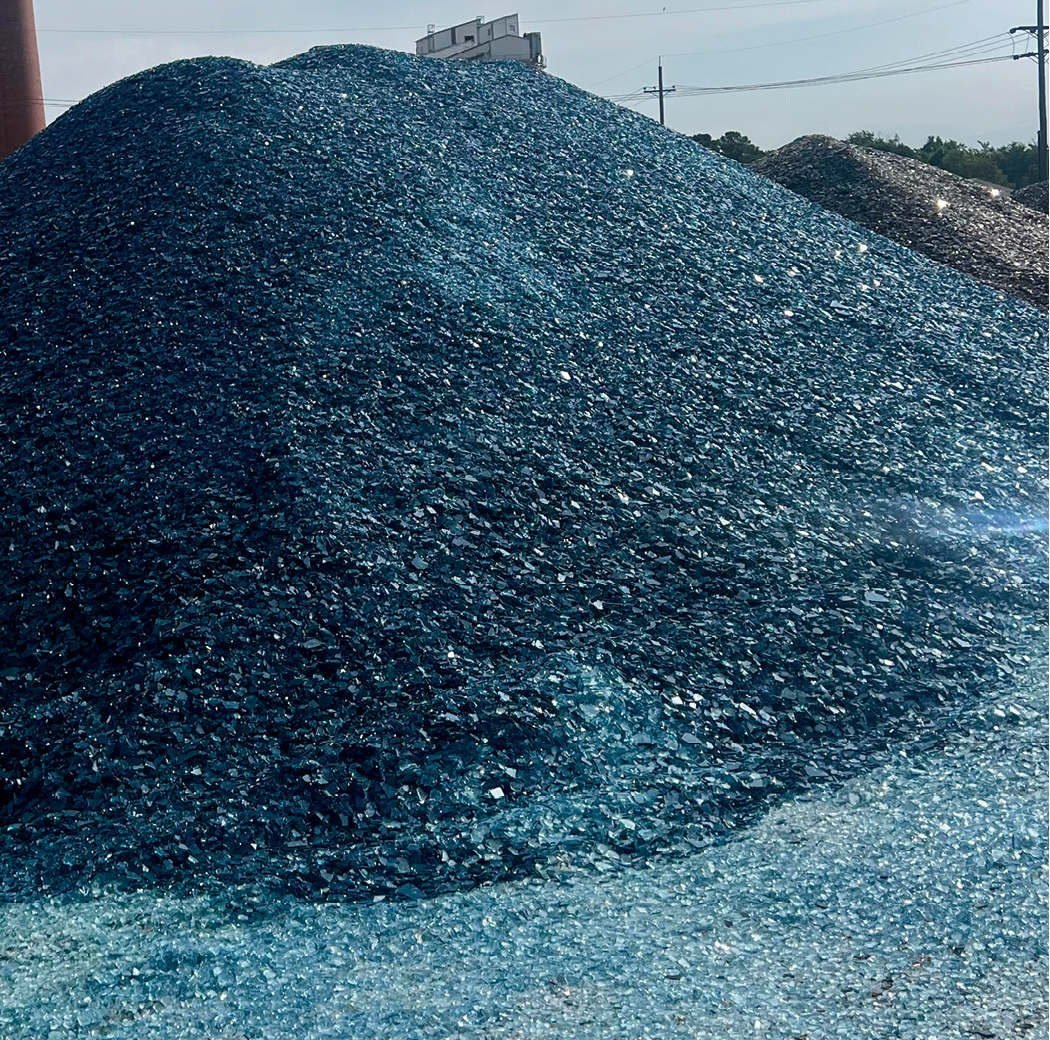
Challenges to recycling in North America
The U.S. recycling rate is approximately 33%, whereas many European countries have achieved approximately 90%. Glass recycling rates are trending positive, and demand for glass waste is increasing. Still, many challenges remain to establishing a glass recycling infrastructure.
Shipping distances to recycling facilities are long, and landfill costs are relatively low in many areas of the U.S.
When it comes to recycling, says Kyle Sword, research and development director of North America at NSG Pilkington, many of the incentives, such as higher gas prices and higher landfill prices in Europe, simply don’t exist in North America.
“The reality is, natural gas [which can be used to manufacture new glass] is pretty cheap in North America compared to elsewhere in the world, landfill costs are pretty cheap compared to elsewhere in the world, and shipping distances are pretty long as compared to elsewhere in the world,” he explains.
Glass companies may not be aware that glass waste or cullet has value.
The cullet waste stream from all areas of the supply chain has a potential market value, but glass industry professionals may not be aware of this. Sword says that many glass fabricators or glass industry companies are still not aware that cullet’s value has changed in the past two decades, and that minor changes to their operations to separate cullet from contaminants could yield high-quality cullet that has value.
Recovery of post-demolition glass remains challenging.
Already installed glass that is removed for retrofit or demolition could be an opportunity for glass recycling. But the logistics and financial cost can be prohibitive, says Austin Beaupré, national supply manager, Resource Recovery, a glass recycler with locations across the U.S. “When it comes to demoing a building, logistics is everything,” he says, from determining who will break down the windows, put them in scrap, transport them and potentially separate glass from other building materials. “It just comes down to a numbers game of figuring out what to do with all of that,” he says.
Infinite Recycled Technologies does retrofit and post-demolition recycling and has found some resistance by demolition crews to the extra work that’s required to recycle glass. “A lot of them don’t take into consideration that as we take that glass for them, we’re doing the hauling, we’re providing the containers and we’re recycling it,” says Patrick Elmore, president of business development, laminated glass recycling.. “They’re saving on the costs of hauling. They’re saving on the container. They’re saving on the landfill costs, which are astronomical in New York, so we’re saving them a lot of money.”
Lack of recycling infrastructure leads to low collection and can mitigate benefits.
Glass recycling should be a part of decarbonization efforts, but a lack of recycling facilities can mitigate those effects in many ways. “Recycling glass is awesome, but if we have to bring a diesel truck and then drive it 200 miles to recycle the glass, it could offset the [carbon] impact,” says Beaupré.
World of Glass map recycling locations
Looking for recycling locations in the U.S.? Search for recycling facilities on the National Glass Association’s new World of Glass map, now on glass.org.
Creating recycling infrastructure in North America is a collaborative enterprise
The recycled glass markets are inter-dependent among many different industries—infrastructure around transportation, cullet processing, cullet storage and local waste management issues like MRFs can all have significant impacts on results. Collaborating regionally, and across different sectors of the glass industry, will be key to creating infrastructure in the U.S.
NSG Pilkington’s Sword is part of the Northeast Ohio Innovation Consortium, a nonprofit comprised of global industry companies, including Owens Corning, NSG/Pilkington and Libbey, which makes glass tableware. The NOIC, designed to encourage innovation across industry partnerships, can help the region better plan for recycling infrastructure and needs, Sword says. By having a broader view of the glass and cullet available in the region, as well analyzing the capacity for cullet production and who can buy and sell it regionally, they can make both the financial and sustainability case for glass recycling, he says, which can then be replicated in other parts of the country.
Courtney Little, founder of Epic Glass recycling and president and general counsel for Ace Glass, started his recycling business in 2018. At the time, the state of Arkansas was collecting about 4 million pounds of glass per year. After he began his efforts at glass collection, that amount grew to 30 million-plus pounds of glass in 2024. He says his goal is that his recycling efforts and local partnerships continue increasing the amount of recycled glass, and that the next step in infrastructure is to work with others to identify gaps in regional recycling.
“Let’s get together and talk about where there’s some regions in the U.S. that are not collecting glass, or [about] what fabricators don’t have an outlet for recycling,” he says. “And let’s find a regional person that can help take that and increase the value of the glass so that it incentivizes a company or a community to collect it and recycle.”
Beaupré adds that shared infrastructure for local recyclers, who may be competitors, may be needed to increase the volume of recycling possible. “We’ve worked with some competitors, and we’ve talked about having shared [material] dumping, sort of shared facilities, where we can work together,” he says. “And if I had to guess, that’s probably where we’ll end up, these companies working together, and then having the locations that we need.”
Infinite Recycled Technologies is also working to ensure that architects are aware and ready to support architectural glass recycling before it’s even installed. Elmore says the company worked with the architectural firm Gensler and top contractors to create a specification sheet for glass recycling. This would control the life cycle of the glass, he says. “So now, when the architects are spec-ing new buildings, they have that language in there already that glass, whether it’s going to be retrofit or if the building is going to be demolished, the glass needs to be recycled,” he says.
Exploring the horizon of circularity and reuse
NSG Pilkington demonstrated the full circularity of glass by recovering cullet from a greenhouse in the UK.
Glass that would have been sent to landfill was remelted and turned into the next generation of greenhouse glass, say officials. This single project led to the recovery of over 220 tons of glass being recycled into new glass products at the company’s float plant in St. Helens, which saved over 55 tons of CO2, according to the company.
“Issues with non-glass products attached to the glass panes and other debris collected from the site were dealt with by working closely with the greenhouse owner to change equipment and monitor the glass removal and collection more carefully, says John Armstrong, logistics, warehouse and quality systems manager.” Working together ensured a much smoother and more successful project, which will benchmark future opportunities. It will also help identify improvements needed in equipment that would make glass recycling more viable on a larger scale when remelting big volumes of cullet becomes an ever more important part of glass production.”
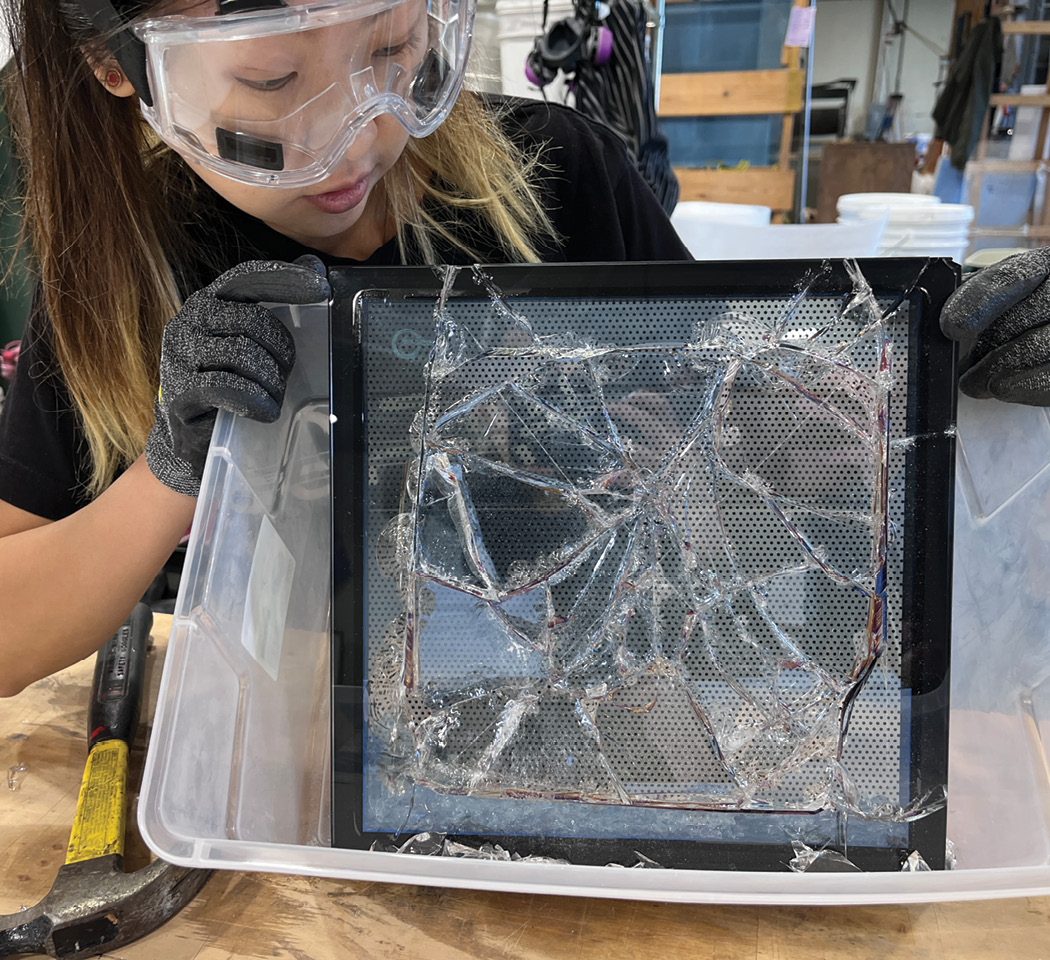
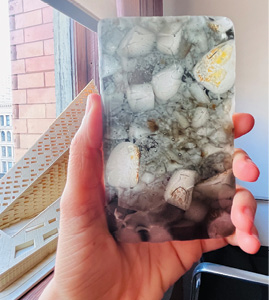
While recycling is one type of reuse, it’s not the only consideration for circularity. Sophie Pennetier encourages the industry to take a long view of decarbonization and reuse, and to consider not just the next iteration of a product, but what its whole lifecycle could be.
Pennetier does not feel a distinction between upcycling or downcycling of material is as important as keeping the material out of the landfill. “I think trying to keep [the material] roughly around the same application is going to be better, [but you have to consider] are you limiting its future recycling potential?” Ultimately, these differences between upcycling and downcycling can be “a potential distraction from what we can do to divert it from landfill,” she says.
Pennetier is actively involved in imagining new possibilities for building materials. This past year she co-authored a paper with Baizhen Yu, “Re-Glass: Product Development Pathways for Post-Consumer Glass,” which examines the viability of recycling soda lime glass from post-consumer insulating glass units. The researchers mixed various types of architectural glass cullet and fused them into flat plates using electric kilns, which melt glass at a lower temperature, thus emitting fewer carbon emissions than a traditional float process.
The research was also designed to find a fabrication method that allows for reprocessing near the site of manufacture, which would further lower carbon emissions by shortening transport distances. The researchers suggest that this type of glass could potentially be used in spandrels, partitions, interior wall cladding and tiling.
Beyond finding new methods of use and reuse for glass, Pennetier also sees potential for expanding online material databases for secondhand construction materials, like Rheaply. Users would be able to search for both new and lightly used products, the latter of which could be certified. “It’s like going to a car dealership for their knowledge. You buy from them because they have the knowledge, not necessarily because they made a new thing for you,” she explains.
Resources from the National Glass Association
This content is partly based on NGA resources:
- FB40-14 (2021), Recyclability of Architectural Glass
- Overcoming Challenges of Circularity and Architectural Glass Recycling (forthcoming)
- Recycling Locations, part of the World of Glass Map
All these resources, along with numerous others about the sustainability and performance potential of glass, are available in full in the NGA store.