Blast Glazing
How trends in blast-resistant glazing change the way contract glaziers operate
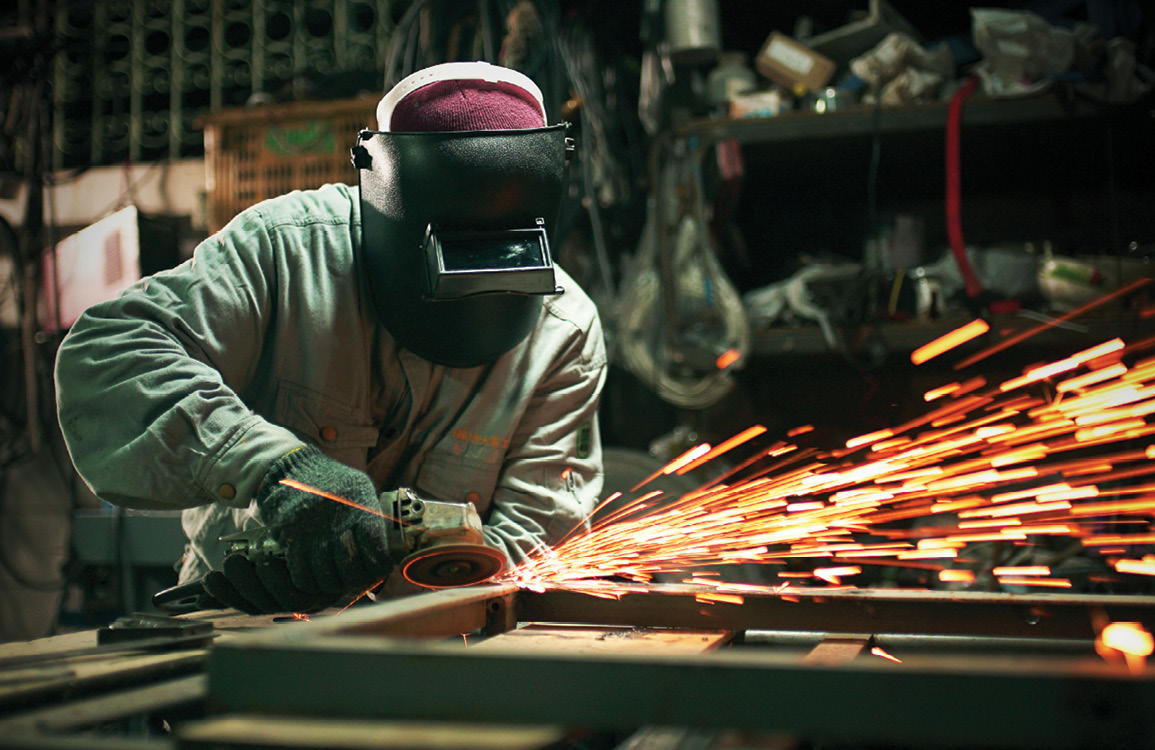
Since 9/11, blast-resistant systems have become a prevalent type of glazing for governmental and institutional facilities. Although this trend has created a new and rapidly growing niche industry within the glazing market, it has also created a multitude of operational complexities for any glazing contractor, no matter the size. This article presents three trends contract glaziers should consider when looking to expand into blast-resistant glazing.
3 blast-resistant glazing trends
1 - Steel, steel and more steel
Blast-resistant façades mean more steel. From simple brackets and angle attachments for punch windows all the way to steel exoskeletons built for progressive collapse, contract glaziers need to understand how steel is integral to their scope of work. Due to this cause and effect, contract glaziers should perform their due diligence and clearly determine whether they have the capability to perform blast-resistant contracts. Whether it is dealing with the supply chain, fabrication, engineering, shop drawings, sealants or even installation, steel can become the structural crux of the entire system.
Although glaziers should not feel they need to have the capabilities to fabricate and erect structural beams and columns, they should have the proficiency to design, fabricate and install the attachments that tie their glazing system back to structure. More importantly, if they want to land larger blast contracts, they should have the capability to do that at scale, whether that means creating a strategic partnership with a steel erector, building a steel fabrication shop in-house, or acquiring a local miscellaneous metals fabricator.
2 - Custom blast loads
In the past, contract glaziers could get away with installing off-the-shelf and pre-tested blast systems on government and institutional projects. These systems were built to accommodate U.S. General Service Administration standard blast loads, and large fabricators had plenty of pre-designed and tested products that were consistently listed as Basis of Design options that could be easily purchased and installed.
As design trends continue to dictate unique and custom façade systems, it has become harder to utilize these off-the-shelf systems for blast resistance. More often than not, prominent public, institutional and governmental buildings have a unique design that requires a custom psi/psi-ms blast load. This situation forces fabricators to engineer, build, test and certify a custom system specific to that project. This process takes longer, costs more money and requires a higher level of engineering capabilities than what would be required if using a pre-tested system. This issue is only compounded on projects with design assist or delegated design requirements, as a great portion of the engineering risk falls squarely on the façade fabricator. Larger fabricators or contract glaziers might have the capabilities to meet these challenges; however, midsize to small glaziers should make sure they fully understand what is required of them before signing up for a glazing system with a custom blast load.
3 - Million-dollar mockups
Many blast projects require mockups. From offsite performance mockups to in-situ visual mockups, the scope, size and cost of the mockups are critical aspects of a project for the glazing contractor. Depending on the size of a project or design complexity, the mockups can have drastic ranges in cost, from a couple hundred thousand dollars all the way up to multimillions.
This trend is especially evident on blast-resistant projects that have custom testing requirements, as mockups can become critical path bottlenecks if the façade contractor is not able to build them, test them and get them approved within the CPM schedule. Without that approval, the fabrication cannot get released and the entire project schedule is impacted.
To achieve that success, glaziers need to have the right experience and capabilities in place, from in-house engineering and design services, to vertically integrated steel supply chains, to blast test chambers, to thermal modeling. The glaziers that can embrace these challenges will be positioned to provide timely solutions to their clients and withstand any force that comes their way.