Challenging Installs
3 installation case studies that show what advanced glass lifting and handling equipment can do
Glass is getting bigger and heavier, and geometries more complex. Glass lifting and handling equipment suppliers have responded with higher-capacity, heavy-duty, more flexible machines to tackle nearly any job. Check out the equipment in action in three case studies.
Curved and Complex at the Denver Art Museum
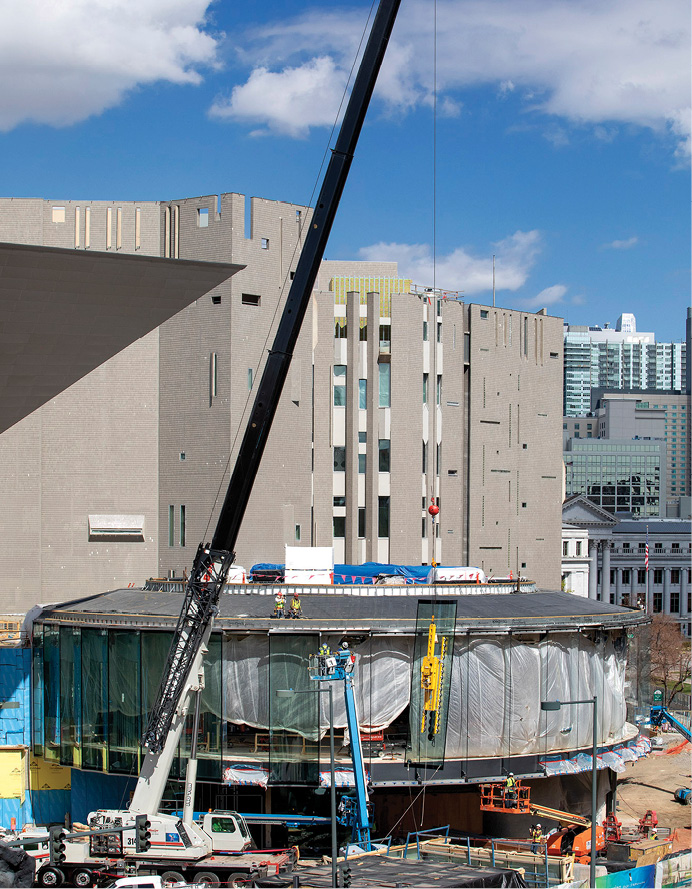
Challenges
An elliptical façade of floor-to-ceiling curved glass lites surrounds the new welcome center at the Denver Art Museum, designed by Fentress Architects. Jobsite logistics and installation of 36 massive curved lites, each 24 feet tall and 8 feet wide, presented notable challenges. The units are laminated and insulating, each weighing 3,200 pounds. However, it was the curvature of the glass that presented the most notable hurdles, says Daniel Meuchel, design engineer for Wood’s Powr-Grip.
The curved nature of the glass “just throws us for another loop. Your [center of gravity] is so far out from the pick point, and your hang angles are different,” says Meuchel. The glass for the museum project hung at a 6-degree angle, due to the size and curve of the glass, he says. Additionally, the glass was to be set from the concave side, requiring more flexible vacuum pads to maintain suction.
Solution
Wood’s Powr-Grip worked with contract glazier Harmon Inc. at the mockup stage to develop a successful lifting solution for the job. The custom vacuum lifter features 32 smaller suction cups to attach to the concave curve. “The 9-inch cups have a lower capacity, but they offer ease of attachment,” says Meuchel. To address the 6-degree hang angle, the team attached a separate vacuum cup to the back of the lite, allowing installers to essentially “pull” the glass into a righted vertical position.
Sizable Storefront in the Hurricane Zone
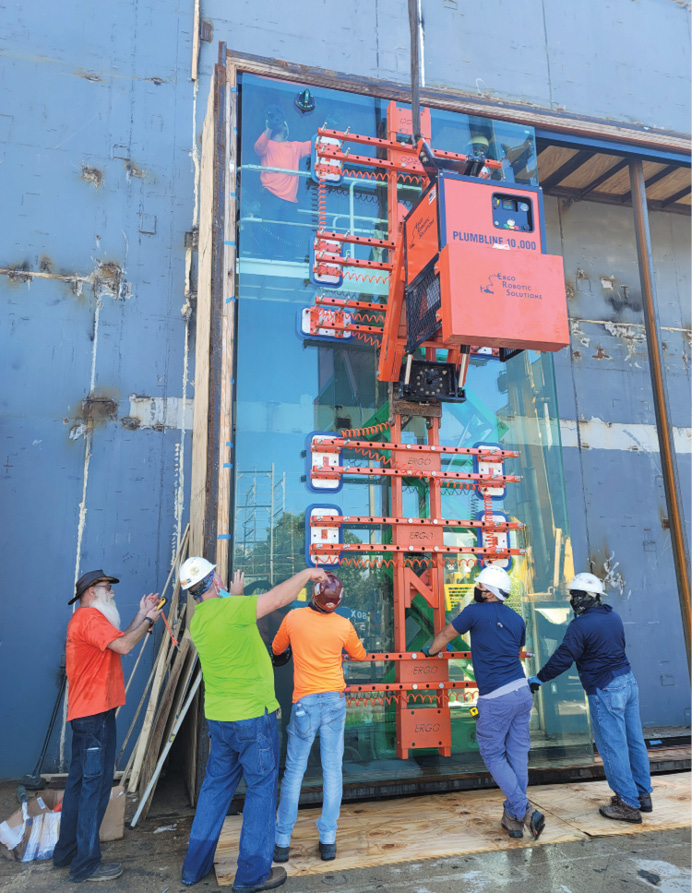
Challenges
Faour Glass Technologies recently completed mockup testing for a specialty installation featuring jumbo glass units that are impact-rated to meet Florida’s more stringent hurricane codes. The job features 20-foot by 10-foot glass lites, each weighing about 5,200 pounds. The glass is 2-inch laminated.
“Due to the massive size of this piece of glass, combined with the weight, we required specialized equipment to handle it. Maneuvering such a huge piece of glass is no easy feat,” says Annette Trevisan Nuhfer, director of sales, marketing and estimating, Faour Glass.
Solution
Faour Glass teamed with Ergo Robotic Solutions to accomplish the installation. “Ergo Robotics was key is this undertaking, as they were able to produce a custom piece of equipment for us to lift and balance the panels as they were set into the frames,” Tresvisan Nuhfer says.
The team used the Plumbline 8000 from Ergo Robotic Solutions to lift and set the glass. The lifter is designed to hold up to 8,000 pounds. It is a below-the-hook unit, meaning it’s hung from the crane, and it was designed to pick up and rotate the jumbo units of glass, says Alan Nudi, director of sales and marketing for Ergo.
“This is huge stuff,” says Nudi. “When you have heavy, very large pieces of glass, it’s not that hard when you know how to do it right.”
Big Reach, Big Glass at Minnesota Home
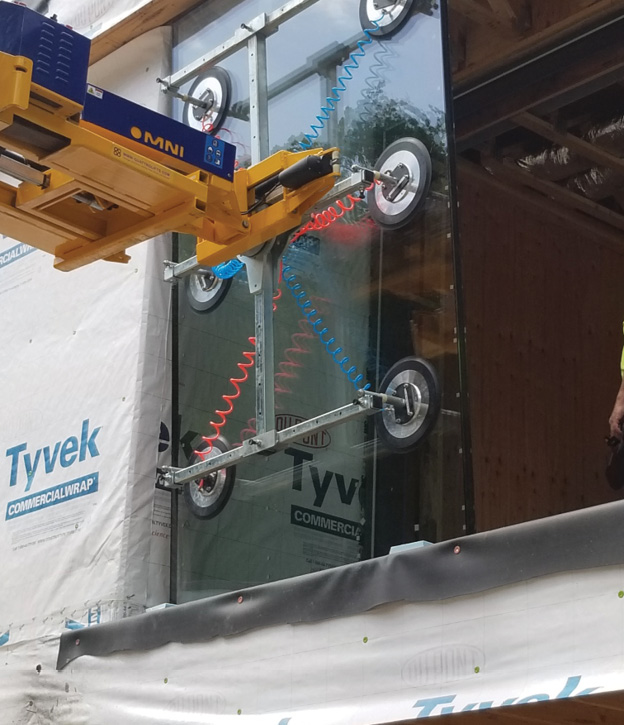
Challenges
For an impressive private residential project on Lake Marion outside of Lakeville, Minnesota, installers were tasked with maneuvering large, heavy, triple-pane insulating glass units around several jobsite obstacles. The project features 70 windows, including 45 large-size units. “The bigger the pieces, the tighter the spaces,” says John Olson, technical support, Quattrolifts. “Architects design with these large sizes, but they don’t realize how difficult it will be for the units to be put in place.”
To reach the glazed openings on the project, installers required equipment that would reach at least 40 feet from the vehicle. To add to the challenge, a structural beam stood in the path of the boom, requiring additional handling precision as installers maneuvered the large panes of glass.
Solution
The project team used the Quattrolifts Omni 1800, attached to a telehandler, to complete the installation. Using the equipment, the team was able to extend the boom and maneuver the glass units over the interrupting load beams to reach the openings. A rotating head allowed for placement of glass units in multiple openings, without requiring the team to move the machine to a different location on the jobsite.
Omni 800/1800 On-site from Quattrolifts on Vimeo.