Consider the Corner
Aluminum entry door corner construction can simplify installation, improve serviceability and extend longevity
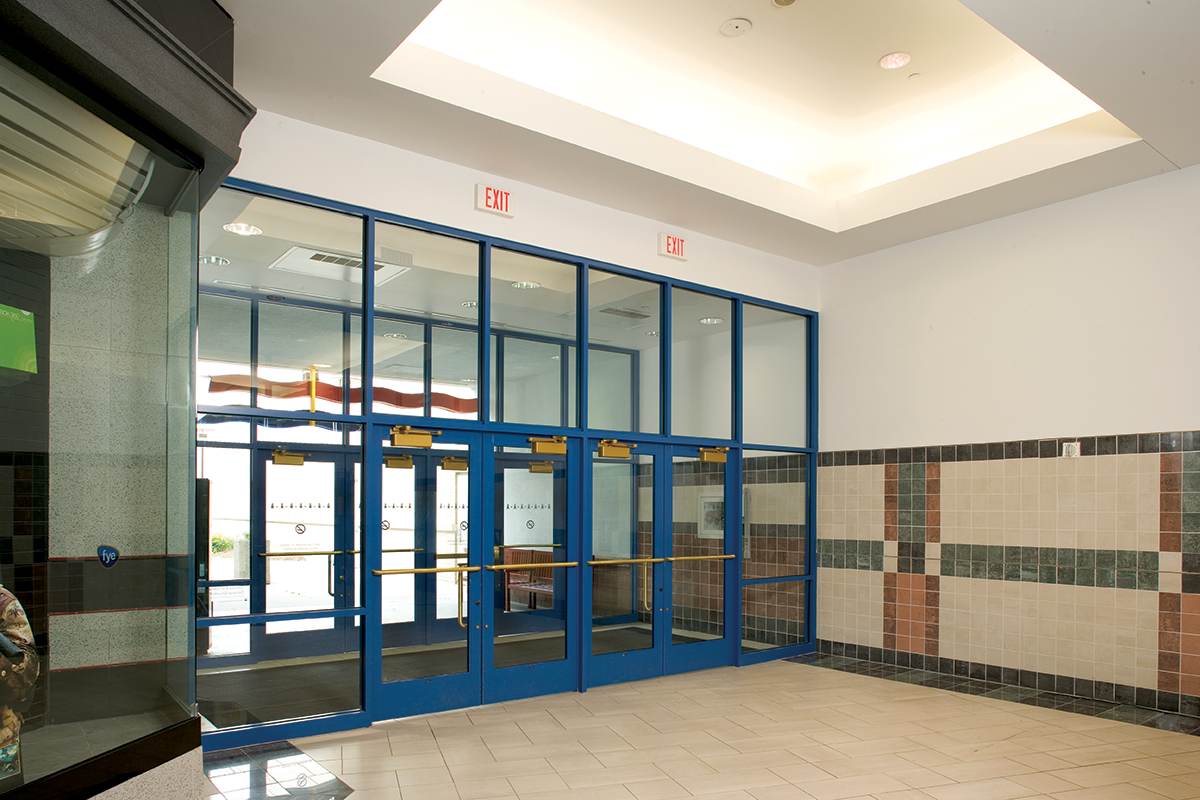
Above: Example of aluminum tie-rod door construction in use at RiverTown Crossings Mall in Grandville, Michigan. Photo by Jeff Tippett, courtesy of Tubelite.
The Bottom Line: Aluminum entry doors with tie-rod corner construction offer better serviceability, flexibility and longevity compared to welded or shear clip designs, allowing easier modifications and repairs, making them a cost-effective, durable option for high-traffic installations.
High-traffic entry doors experience hundreds of thousands, or even millions, of openings and closings every year. They are one of the hardest-working elements of a building—a moving part with loading typically concentrated on two small hinging sites.
In an aluminum door dominated by glazing, the outer perimeter of the door must do the structural work. The thin outline-framework of extruded aluminum is made of vertical members called stiles and horizontal members called rails, which are joined at the corners. The strength of a door depends on the strength of its corners.
Most aluminum doors are made using one of three methods:
- Tie-rod construction uses steel rods across the top and bottom of the door. The rods are anchored in the vertical stiles and thread through the horizontal rails, tying the stiles to each other with the rails gripped in between. The rods have threaded ends and are secured with locknuts on both sides.
- Welded corners have a bracket screwed onto the stile and then welded to the rail.
- Shear clip corners have a small piece of aluminum channel fastened to the stiles and then bolted to the top and bottom rails.
Doors with welded and tie-rod corner construction methods are equally durable. However, they have different advantages within manufacturing. For example, a welded door eliminates the material cost of the tie rod. On the other hand, a tie rod door does not require the set up and skilled labor necessary to fabricate a welded unit.
Considering installation, serviceability and longevity for the doors, tie-rod construction offers great savings and flexibility. If the door needs to be modified, or if parts need to be replaced, tie rods can be unfastened, and the door taken apart without diminishing its structural integrity, durability or finish.
There are millions of aluminum entry doors installed across the country, and some have been in service since the 1950s. Tie-rod doors can be refurbished, replacing worn parts. An installer can adjust the glass blocks and fasteners to bring door leaves back to square with the openings. Replacing the weatherstripping and seals optimizes air tightness. Worn-out individual elements, such as a rail or a stile, can be replaced on tie-rod doors. This approach may be considerably less expensive than a full replacement.
When a high-traffic door must be replaced or updated performance is desired, it does not mean the end of its life. Old doors can be reused in low-traffic applications, and tie-rod doors can be disassembled and used to repair similar doors.
A final purpose for aluminum door components is to recycle the metal for other construction materials or other products. Aluminum can be recycled with no loss of metallurgical properties and is one of the major reasons that aluminum remains an affordable, dependable architectural material.