Determining an Acceptable Color Variance for Decorative Glass
Measuring color tolerances with solid uniform color applied as a pigmented coating or interlayer
Excerpted from NGA Glass Technical Paper FB77-24 Determining an Acceptable Color Variance for Decorative Glass. Download the complete document for free.
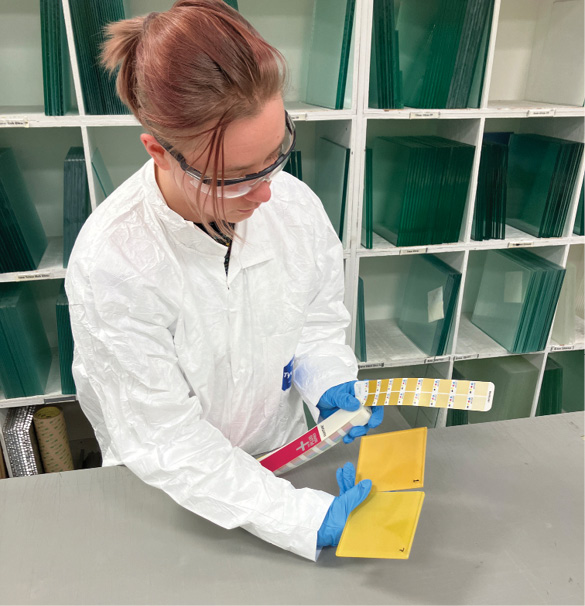
There are variances in all production processes. Manufacturers minimize variance to an acceptable limit with process and quality control. Decorative glazing is not exempt from variance; the overall color of the decorative glazing is the result of the compounding factors of the decorative components and the processes used to make them. This Glass Technical Paper establishes a voluntary measurable industry acceptable color variance for decorative glazing products that could be used as a baseline for specification. This document is not meant to replace or supersede job requirements or override specific vendor specifications.
Scope
This document covers measuring color tolerances, both reflected and transmitted, of decorative glazing with solid uniform color applied as a pigmented coating or interlayer. Decorative glazing with solid patterns or graphics may not be measurable with the methods covered in this document and, therefore, is outside of its scope.
Scenarios for defining color tolerance
When measuring a color difference between two materials, one being the control specimen and the other the trial sample, it is important to recognize that this measurement can only be made between two similar materials. The control specimen is the agreed-upon color, whereas the trial sample is the specimen being compared to the control. Measuring a glazing sample against any dissimilar material, such as a paint color chip, is challenging and may not yield appropriate data as the two materials behave differently in the measurement device and may give different readings.
Accepted target to final goods—The accepted target (sample/ target/ mockup) is compared to final goods (the product in question). Because of the extended length of time between sampling and construction, there may be variation in color as raw materials may have changed from the time of sample manufacture to the time of final production within the tolerance of the raw materials being used. For example: glass, interlayer, film and inks all have independent variances and add complexity from the compound impact of these material differences on each other.
Batch to batch—Materials for larger projects may be made in multiple production batches. Batch color should be compared to the original approved sample. Differences in batches can be mitigated through planning materials and installation schedules to install pieces from common batches together. Replacement glass would not be considered an additional batch but would require a new sample for approval.
Internal batch tolerances—When items are made at the same time with controlled raw materials, the color tolerance from one piece to the other has a closer expected color tolerance than the previous situations. Batch color should be compared to the manufacturer’s internal production target.
Equipment to measure glass color
A handheld spectrophotometer can be used to measure reflected color, is designed to be portable, and is therefore suitable for use in a glass fabricating factory or at the building site before or after installation. The near normal reflected color of the glazing is measured and converted into a numerical value. The instrument must have an integrating sphere and measure color with the specular component included from the built-in light source. The instrument has color data storage and a small display of the actual color measurements. A software package is typically supplied to manipulate the data, calculate Delta ECMC values (difference in color between two measurements), and graphically display the color data.
A second option is a benchtop spectrophotometer, which could measure both reflected and transmitted color. However, this can only be done on small sample sizes because the glass is staged in a closed chamber to block out all external light. These instruments are much larger than handheld instruments and more suitable for a lab environment. Because benchtop spectrophotometers are considered more accurate and precise than handheld devices, they are often used to establish the standard color targets and samples to which the handheld devices can be compared.
Suggested Color Tolerances
For the purposes of this document and setting a quantifiable measurement for quality control, the Color Measurement Committee calculation is recommended as it has been adopted as the calculation of choice for many other materials for Delta ECMC between 0 and 5. This will allow decorative glazing to be consistent with other materials in the design world.
A consideration for determining color tolerances in a product is the ability to control the color of the raw materials. There is always some tolerance in raw materials, which varies by material type. This includes glass, interlayers, decorative coatings and pigments.
The table below shows suggested color tolerances according to base substrate.
NGA thanks our task group volunteers for developing this resource: Michael Saroka, Goldray Glass–chair; Dan Laporte, Mativ; Paul DiCesare, Vitro Architectural Glass; Jeff Nicholson, ICD High Performance Coatings; Kayla Natividad, Pilkington North America; Julia Schimmelpenningh, Eastman; Randy Reynolds, Glass Coatings and Concepts; Vaughn Schauss, Kuraray America; Marc Deschamps, Walker Glass; Jon Griggs, Guardian Glass; Nicholas Karpa, Glass Coatings and Concepts; Aaron Thompson, Viracon; Jim Gulnick, McGrory Glass; Jason Fisher, Oldcastle BuildingEnvelope; Thomas Wojtowicz, Viracon; James Wright, Thompson Innovative Glass; Bobby Chestnut; Michael Morrissey; Kevin Ramus; and Rick Wright.