The Digital Factory
The why and how of automation and integration on the glass factory floor
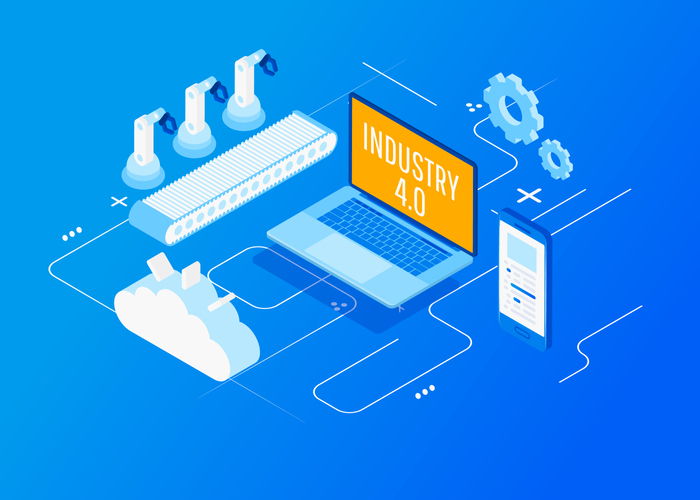
There is no shortage of terms when it comes to digital advancement in glass fabrication. Smart Factory and Industry 4.0; the internet of things (IoT) and the industrial internet of things (IIoT); digitalization and intelligentization; artificial intelligence (AI), radio frequency identification (RFID), enterprise resource planning (ERP); and so many others.
While the vocabulary can get complicated, the takeaway is the same. The glass fabrication industry is rapidly moving toward a more automated, integrated, digital world. “I have been in this industry for 44 years. It’s one of [the] slowest-moving industries. But we’re seeing changes. We’re seeing things moving quicker and quicker,” says Michael Spellman, president, IGE Solutions.
Discussions of factory advancements have only accelerated during the pandemic, as companies tackle labor shortages, supply chain disruptions, delays for service and replacement parts, and more. However, the path to digitalization is complicated and may look different for each company.
This article presents a high-level look at the digitalization of the glass factory, answering two fundamental questions for company leaders looking to make investments. First, why should a glass fabricator invest in new digital solutions? And, how can a company successfully incorporate digital solutions?
This article is based on one-on-one interviews with experts and on conversations among industry leaders during the “What’s Trending in Manufacturing” webinar from GlassBuild Connect, now available on demand.
Why?
-
Do more with less
“Labor has been the biggest pain point for the last decade or more,” says Spellman. Factory automation can help.
“As the labor shortage has proven, you can’t throw more people at a problem and expect to solve it,” adds Chris Kammer, marketing coordinator, A+W Software North America. Through automation and software integration, fabricators look to move away from manual processes while increasing productivity, efficiency and consistency across the factory floor. Doing so reduces the number of operators working on a production line, employees required for handling and transporting glass in the factory, workers inspecting glass and more. “People are reluctant to change, but change is the only way we advance,” Kammer says.
-
Prioritize preventative maintenance
Digitalization of the factory allows companies to closely track machine performance and production data, notifying operators and managers of maintenance needs before parts or systems fail. “A lot of quality is driven by how well machines are working,” says Dave Miller, business development, FeneTech. “One advantage you get when you’re running through a software system is metrics. You can track the linear inches of polishing, or square feet of washing or tempering, to give a metric of when to perform maintenance. This keeps the machines working better in the long run.”
-
Ensure consistency
“Trying to get consistency with manual systems is very challenging,” says John Bush, head of John Bush Consulting Inc. This has been a major driver for glass companies when making investments in automated solutions, particularly for inspection and quality control checks.
“We’re seeing a bigger effort on [adopting automated] systems for checking quality,” says Miller. The systems replace manual quality checks, which can lead to inconsistencies from operator to operator. “Companies can use an automated system to electronically detect defects and alert operators, allowing the operators to make the decision. Or, you can set a threshold within a system to automatically issue a remake,” he says.
-
Manage remakes
Some fabricators are introducing automated quality checks during early stages of the process. They catch quality issues earlier in the process and can trigger remakes more quickly, thus saving time and money. “If you wait until after tempering, or when you have a finished product, to do quality checks, you’ve already spent time tempering that unit, taking time away from a good unit that could have gone through tempering,” Miller says.
-
Tackle larger sizes
“It’s a challenge to automate systems and equipment to create fabrication techniques that work for oversized glass, large glass,” says Rob Carlson, engineer/designer, Tristar Glass. Large sizes, while growing in popularity, remain a niche product for many glass fabricators. However, companies increasingly find themselves investing in equipment to handle the large sizes. “It comes down to things like safety and workforce. If you have people handling those larger units, picking those up, it becomes a safety factor,” he says.
How?
-
Connect the islands
Many glass fabricators have already transitioned to automated machines across their factory floors. The challenge then becomes “tying the islands of automation together,” says FeneTech’s Miller.
“One of the big pushes for many fabricators is getting information to flow freely from one work center to another, so you don’t have additional data entry, you don’t have to worry about information that’s mistyped, you don’t have mistakes that require work to be redone,” Miller says.
-
Plan production
Use digital tools to most effectively plan production across all lines on the factory floor. This helps fabricators address lead time challenges and ensure on-time delivery, no matter the product type.
“We’re looking at glass for insulating units, glass with laminated lites, glass that can be cut and tempered, glass that requires hole drilling. In short, you have a lot of different processes and a lot of different lead times,” Miller says. “One thing we often help customers with is managing production lead times with target shift dates to ensure each component process starts at a time to be completed on time.”
-
Don’t get buried in data
Smart factory solutions allow fabricators to track numerous metrics, which can leave plant managers digging through data. “There is an enormous amount of data that can be collected. If you start an Industry 4.0 process without an end goal in mind, you’re going to end up with a needle in a haystack. You have to know what you’re trying to achieve [through data analysis] and collect that data,” says Ron Crowl, president, FeneTech.
-
Track what’s important
Fabricators should begin by prioritizing data collection. Miller recommends companies determine the most important issues, or problem areas, to address on the plant floor, and then track data that directly relates to those issues. “What is the metric that you can measure to fine tune that bottle neck? Or, if you see most of your rejects occurring in tempering, you probably want to measure things there,” he says. “Narrow your focus. Address the [key performance indicators] first.”
-
Focus maintenance tracking
Similarly, fabricators should focus their data collection when it comes to preventative maintenance. It’s easy to collect too much and miss warning signs regarding parts replacement or other service requirements.
“You need to be able to see motor averages—see when things are changing from the norm. But with a machine that has 50, 60 motors, you’re getting an awful lot of data,” says Bush. Setting limits and parameters within the automatic system makes tracking easier, he says.
Fabricators should also track wear and age of parts, says Mike Willard, CEO/owner, Salem Fabrication Technologies Group Inc. “Track the diamond wheel life, core drill life, routers. You can anticipate when those have to be changed,” he says.
Smart Factory Solutions at GPAD
GPAD—Glass Processing Automation Days—provides a unique two-day opportunity to investigate new and innovative technologies in the glass fabrication industry and to discover the additional benefits of automation and integration. GPAD was founded in 2013 by FeneTech Inc.; NGA took over as organizer in 2019, with FeneTech recognized as a “Founding Partner.”
GPAD returns in 2022, March 29-31 in Nashville, where glass fabricators can meet up with industry machinery, equipment, tool and software suppliers to discuss advancement on the factory floor.
“At GPAD, the very focused topic of complete factory automation and integration is about futureproofing,” says Nicole Harris, president and CEO of the National Glass Association. “GPAD’s sponsors present solutions in a classroom setting, and the conversations continue during relaxed social gatherings with fabricator customers and prospects. The intimate size and focused scope of GPAD make for meaningful exchanges to build relationships; proof is in the repeat attendee list.”
“I’ve only been able to attend that one GPAD event, which took place pre-pandemic in San Antonio,” says Don Power, vice president of manufacturing for Aldora. “What came out of that first GPAD meeting for me was a new laser logo machine, new digitizing software, and some great ERP discussions—all of which has helped our business tremendously.”