Fabricating Flat Glass Mirrors
Mirrors provide both functional and aesthetic performance
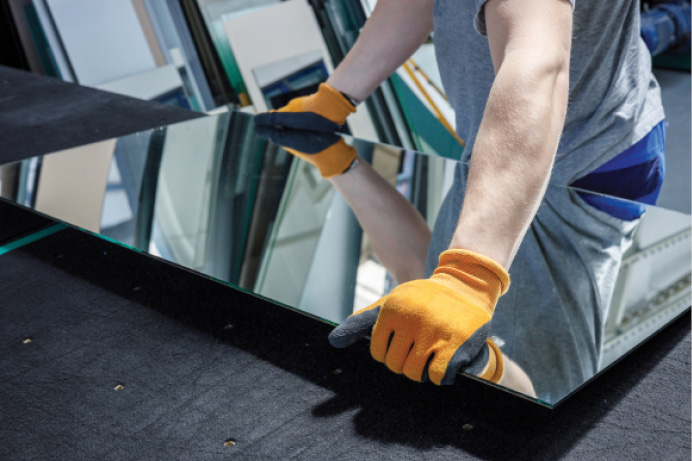
Mirrors provide both functional and aesthetic performance in interior design for homes, office buildings, schools, medical and institutional facilities. In addition to the function of providing reflected images, mirrors are used to move natural light further into buildings and enhance the openness of rooms.
Silvered flat glass mirror products can be fabricated to provide additional aesthetic appeal, such as beveled edges and surface accents. As additional fabrication features are applied, it is critical to ensure proper fabrication conditions and techniques are utilized during every step of fabrication to protect and maintain the integrity of the mirror backing and edges.
General mirror fabrication guidelines
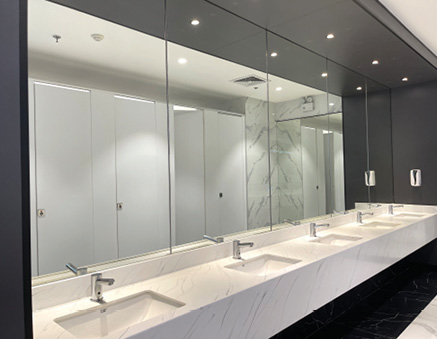
Consult with the mirror manufacturer for any special requirements that may need to be followed during fabrication.
Whenever possible, mirror fabrication should take place in the environment of a fabrication shop or glass distribution facility. Mirror fabrication operations should be located in an area away from exposure to solvents, heavy-duty cleansers and other materials or chemicals that can damage the mirror backing.
Fabrication areas and equipment should be frequently cleaned to prevent exposure to dirt, grit, solvent or other contaminants that could damage both the glass and mirror backing surfaces. Mirror glass may be cleaned with automated glass washing equipment or by hand. Avoid any cleaning products described as highly acidic, highly alkaline, abrasive, harsh, and/or aggressive.
The mirror manufacturer may recommend specific cleaning solutions for the edges and backing, for example a mild phosphate-free detergent with neutral pH or water with 20% isopropyl alcohol.
All cutting table and fabrication equipment surfaces that contact the glass and/or mirror backing surfaces should be frequently vacuumed or swept to prevent scratching or other surface damage. The mirror manufacturer may provide a list of compatible cutting fluids. Glass handling gloves should be worn by all individuals handling mirror products before, during and after fabrication. Gloves prevent skin oils, body salts and chemicals from contaminating the edges.
Clean, fresh water with a coolant is the best lubricant for grinding and polishing operations. The solution should be pure with the pH maintained between 6 and 9. If coolant tanks are used, the water should be changed often enough to prevent biological growth. The solution temperature should be maintained below 100 degrees Fahrenheit (38 degrees Celsius). The mirror manufacturer may provide a list of compatible grinding coolants.
Fabrication wheels should be centered over the edge to minimize excessive grinding on the mirror backing. Diamond wheels should always be dressed and maintained in good cutting condition. When using a belt sander for manual grinding and polishing operations, it is preferable to use a wet operation.
When manually dry-belt sanding, caution should be given to the fact that some belt lubricants contain chloride contaminants. Both dry- and wet-belt seaming should be in a direction from back (paint surface) to front. Grinding or polishing wheels should be used in one direction only, either parallel with the edge (such as with a peripheral wheel) or from back (paint side) to front.
Heat generated by sanding and swiping should be minimized to prevent damage to the mirror backing.

Heat-treated mirror products
If product applications call for the use of heat-treated mirror products, glass surface and edge fabrication must take place prior to the heat-treating in order to maintain proper surface and edge compression required for the safety glazing material. Silvering operations take place after heat-treating.
Handling mirror products
As mirrors are handled following fabrication, do not slide mirror or glass surfaces over each other as permanent scratching or other damage may occur.
Following fabrication, all mirror backing, edges and glass surfaces should be thoroughly and promptly washed and dried. It is very important that all traces of coolant and polishing compound are removed from the edges. If left in place, they are a contaminant that can cause black edge. Black edge refers to damage to the mirror edges caused by liquid contacting the edge.
For vertical wall applications whenever possible, retain at least one factory cut edge of the fabricated mirror for installation at the sill (bottom) where the mirror may be subject to condensation puddling.
For mirror glass that has been cut, sanded, polished or beveled, the mirror manufacturer may recommend sealing the edges with a compatible neutral pH edge sealant.
Learn More
This excerpt is from a technical document developed by member volunteers and subject matter experts from the National Glass Association, available for free download.