Flat Glass Recycling and Sustainability
Demand for recycled glass material is high
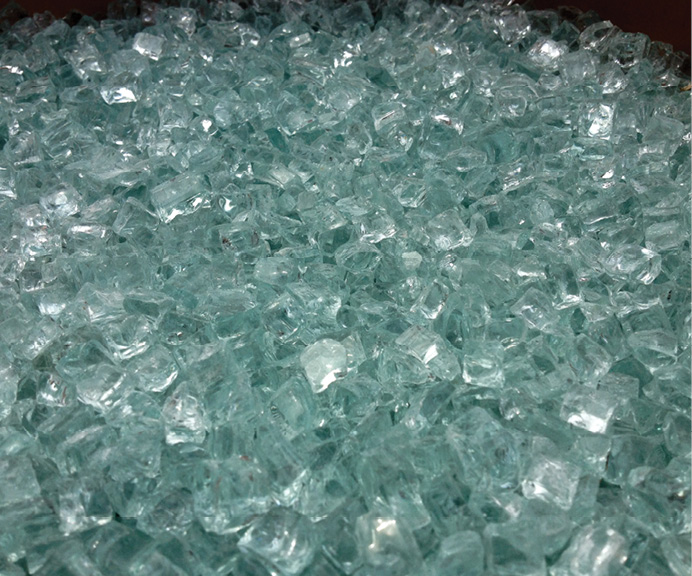
Demand for recycled glass material is high, giving scrap glass generators an opportunity to find a better environmental and economic alternative to discarding glass in a landfill. A wide variety of architectural soda-lime glass products can be recycled. Annealed, tempered and low-emissivity glass can be recycled with virtually no restrictions. Technology has evolved so that historically harder-to-recycle glass products—such as laminated glass, back-painted glass, mixed tints and mirror—have also become routinely recycled.
Recycled glass supply chain
The glass recycling supply chain begins with a glass fabricator shipping its glass scrap to a recycling facility. The recycler mechanically cleans, crushes and screens the glass to create a uniform material. This material is generally sold in bulk to an end user or manufacturer where it is melted for use in a derivative product, such as glass containers (jars and bottles), road grade, fiberglass, reflective highway paint, landscaping products, countertops and coastal restoration materials. Occasionally, a glass recycler grinds the material to a fine powder to sell for use as a filler or an abrasive. Quality specifications and the value of the recycled glass scrap can vary based on the market, end customers and fabricators.
Working with a local glass recycler
The first step in building a successful recycling program is finding and communicating with a local, knowledgeable glass recycling company. Due to the weight of glass, the proximity between the glass fabricator, the recycler and the end user is important. Glass fabricators can establish a working relationship with the nearest glass recycling company. This can help to lower freight costs and drive the highest value for the recycled material. Recyclers typically accept glass from a spectrum of suppliers and industries beyond architectural glass fabricators. They work with automotive, solar, appliance, electronic and other industries and therefore are knowledgeable of how to leverage value across many different end markets.
Contaminants
Most glass scrap generated by an architectural glass fabricator can be recycled if attention is given to avoiding cross contamination. Prior to shipment, fabricators can work with their recycler to define the best way to segregate their scrap to ensure positive value and acceptability.
Glass recyclers can process most contaminants, such as small amounts of metal, aluminum or plastic frames; plastic films; temporary protective film; refractory or rocks; caulk; rubber gaskets; etc. Potentially unacceptable contaminants that could be rejected are lead-based paints, desiccants, and hazardous or heavy metal material. Mixed glass compositions like borosilicate and glass ceramic must be segregated out from soda lime glass. It is important to communicate with the glass recycler to understand what types of glass and what levels of contamination are acceptable for recycling.
Returning recycled glass to the float process
Ideally, recycled glass, or cullet, would be re-melted in the float glass process. Using cullet in the float glass furnace has multiple benefits:
- Reduces the amount of virgin material mined from the ground.
- Reduces the exhaust gas and carbon dioxide from material conversion. Typically, it takes 1,170 tons of batch to make 1,000 tons of glass. Approximately 17% of the weight of the batch is lost through the conversion of oxide batch materials into the glass phase. The loss creates carbon dioxide, nitrogen oxide, sulfur oxide and other gases.
- Cullet is easier to melt, so the amount of energy used to melt one ton of usable glass is reduced.
Unfortunately using cullet from outside the float glass facility introduces risk to the process and the resulting product. Contaminants in recycled glass cullet could compromise the float bath equipment and negatively impact the quality of new glass, leading to downtime and equipment repair if extreme care is not taken. Aluminum and nickel are two of the most concerning elements, but all types of contamination could cause serious damage to a glass furnace and the architectural glass products produced.
Aluminum and nickel
Aluminum contamination doesn’t fully melt and absorb into the glass melt. Aluminum stays volatile and floats on the surface of the molten glass, rapidly volatizing and causing millions of bubbles. The only way to eliminate this contaminant is to physically remove the volatile material floating on the surface, which is extremely complicated.
Nickel is a serious contaminant as it can combine with sulfur in the furnace fuel or the batch materials to form nickel sulfide inclusions. In annealed glass, these are harmless, but during the processing of fully tempered glass, the nickel sulfide inclusions may transform into a state wherein they will expand irreversibly with time and temperature. The expansion may produce sufficient stress to cause spontaneous glass breakage later. The only way to avoid nickel oxide is to eliminate the use of any nickel or nickel-containing materials in all portions of the supply chain. This not only means eliminating nickel as a raw material, but avoiding all nickel containing materials, such as certain types of stainless steel in the transportation, conveyance, weighing and melting operations.
Next steps
Glass is infinitely recyclable and the need for recycling architectural glass will continue to grow. New recycling technologies and facilities will open in different markets as demand for architectural glass recyclers increases. This growth will be spurred in part to reduce energy consumption and carbon dioxide emissions and in response to the continued demand for recycled products by consumers.
The National Glass Association’s Sustainability and Recycling Task Group is prioritizing comprehensive recycling of architectural glass materials. By presenting a compelling case for the environmental, economic and societal benefits of recycling architectural glass, this task group aims to advocate for a shift within the industry by dissecting the current challenges, risks and obstacles hindering the efficient recycling of glass. With an in-depth analysis of waste supply chains, the task group will identify key areas of improvement and strategic interventions to effectively facilitate the upward movement of cullet within the supply chain, ultimately fostering a more sustainable and circular approach to architectural glass production and use.
To learn more and get involved, visit glass.org/advocacy/get-involved/committees.
Resources from the NGA