How to Stay Efficient and Maintain Uncompromising Quality
Follow these 3 manufacturing best practices
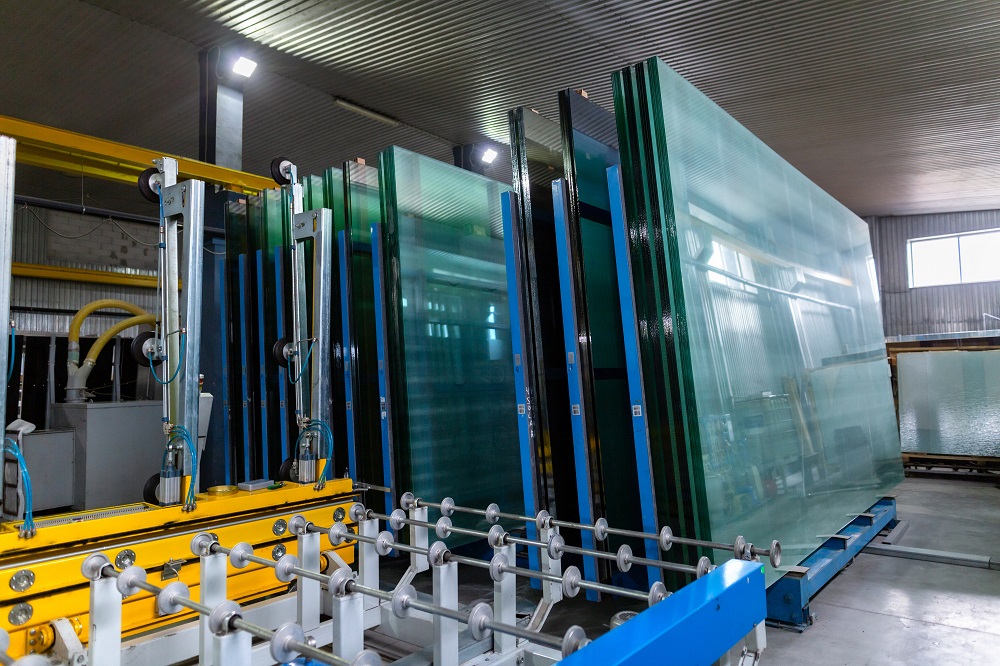
Continuous improvement is essential in any manufacturing environment. It’s the key to efficiency, quality and profitability.
That’s why a fabricator should periodically take a step back identify areas to evaluate and potentially improve throughout the production line. Not sure where to begin? Here are a few best practices a company can leverage in some critical areas of the production process.
Optimize your line layout
An efficient commercial glass manufacturing line follows as straight a line as possible from start to finish, enabling the easy transfer of materials from one point to the next. If, for instance, you’re not following a straight path in carting glass to the insulating station, you’re wasting time. This may seem small, but such losses can add up, dragging down your rate of production.
Small inefficiencies can creep up on any manufacturing process. If you’ve experienced turnover, added new equipment or introduced a new product, one process or another may have become inadvertently complicated without anyone even realizing.
What’s more, your evaluation process might not mean changing what you’re currently doing, but rather discovering that your standard processes aren’t being upheld. Regular auditing can help you uncover trouble and fix it before it costs you.
Identify common problem areas
When it comes to the physical production of insulating glass units, a few particular areas stand out as common error points:
- Desiccant. If your desiccant is compromised, even expertly sealed IG units will show condensation in the air space shortly after it’s been assembled. Your desiccant’s ability to absorb moisture is finite, and most desiccant materials have a strong affinity for ambient moisture, even at low humidity levels. In order to prevent your desiccant from wasting it’s capacity, keep it properly stored at all times. If you’re leaving your desiccants out in the open when your line isn’t in operation, it could become a problem.
- Primary seals. It’s important to be sure your primary sealant is properly placed and not over- or under-filled. Avoid skips or voids in the primary sealant, as this is your main moisture barrier. Next, the joint of the spacer must be fully closed—if the spacer ends are not properly joined, this could create a path for moisture or desiccant to get into the air space. Once you’ve pressed the unit, verify that the primary sealant is fully pressed out and wetted to the glass and spacer. Fully wetted PIB should be a solid, flat black.
- Secondary seals. Your secondary seal ensures the structural integrity of the unit. Your spacer should be consistently inset to allow for a proper secondary sealant depth. Next, be sure that your inset is properly filled. Sealants can sometimes flow up the sides of the glass first, making it look as though the inset is fully filled—but the center may in fact be much shallower. Once the proper depth is achieved, check for and close any joints or gaps, and fix any bulges that extend past the glass edges.
Your production technicians should be well-versed on common production pain points like these. If they aren’t, it may be worth investing some time in training from a knowledgeable third party.
Stay focused on maintenance
Any part of your manufacturing process—whether it’s manual work or a fully automated line—is only as good as what you put into it.
For example, if your crews are loading dirty or roughly cut glass into your machine, it’s likely you’ll have aesthetic issues or possible seal failure no matter how sophisticated and efficient that machine is. What’s more, fixing or remaking poor quality units will eat into any efficiencies you may have gained by investing in automation.
Roughly cut or dirty glass is typically the result of a maintenance lapse. Regular inspection of your glass cutting machine blades is essential to achieve consistent, cleanly cut glass. If you’re skipping this inspection, you may not realize your blades are too dull until it's too late. The same goes for your glass washing station—it’s not uncommon to find that a glass washer’s brushes are not even coming into contact with the glass, or that the machines are using dirty water. These are the kinds of issues that can be easily missed if you’ve put off maintenance tasks for too long.