Keeping Cost and Durability in Mind in the Pursuit of Sustainability
The Bottom Line: As a confluence of forces has made holistic sustainability a priority for new commercial construction, architects need to balance cost and long-term durability of specified components to make it a reality.
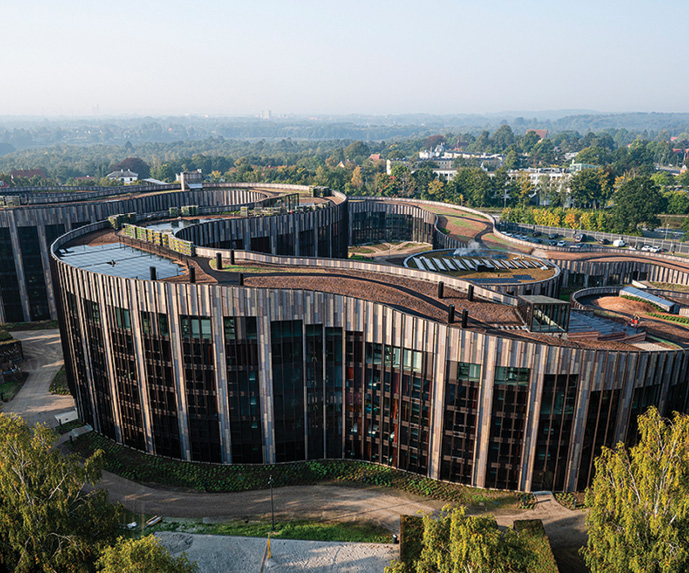
Sustainability has been on my mind recently. Between conversations I’ve had with customers and some potential change coming with the new presidential administration, I expect we’ll be talking a lot about sustainable commercial buildings in 2021 and in the coming next few years.
Consider a few converging forces: President Biden’s agenda includes significant investment in sustainability initiatives, including the goals of constructing 1.5 million sustainable homes and housing units and better weatherizing 2 million homes within four years. The plan is similar to the American Institute of Architects’ “Blueprint for Better” plan, which sets the target of attaining net-zero carbon dioxide emissions from buildings within the next two decades.
Meanwhile, independent of these developments, I’ve heard increasing industry chatter about the Passive House standard in the multifamily and commercial space. The building efficiency that can be realized by applying the certification’s principles has evolved from niche to mainstream and is being pursued by more and more developers.
Commercial glass and glazing play a critical role in many of these goals, and the ever-present challenge of achieving high performance in a cost-effective manner is something our industry will have to contend with. In addition, holistic sustainability is about more than just thermal efficiency—it’s about performance that can be trusted for the long term, without failure and the need for costly replacement.
Affordable sustainability
While highly efficient products are often associated with high costs, consider that Passive House specifically has been steadily growing in an area one might not at first expect: affordable housing.
An instructive example is found in the Belfield Townhomes in Philadelphia, a complex of row houses for residents with low incomes. Completed in 2012, it was the first certified Passive House project in the city, and its success helped ignite a growing trend of highly efficient, affordable housing construction.
By dramatically reducing utility costs via Passive House principles, the building can remain affordable for the long term. It is a sound investment in the Philadelphia community that is set to serve generations of families over the coming decades. Architect magazine describes how the project stayed within its budget by using a simplified building envelope, modular construction and the specification of economical interior finishes.
More recently, East Harlem’s Sendero Verde, the largest Passive House project in the United States, completed phase one of construction in late 2020. When completed, the 360-unit affordable housing complex will feature triple-glazed windows, mechanically ventilated spaces with energy recovery, and other highly efficient technologies to ensure low cost of operation for the long term.
Projects like these demonstrate that creating highly efficient, sustainable structures can be accomplished without astronomical budgets. Specifying high-performance products where they can have the greatest impact—including a building’s glass and glazing—can contribute to the highest levels of sustainability and long-lasting cost-effectiveness.
Longevity through durable technology
In creating sustainable buildings, our industry also needs to be considering technology that is not just thermally efficient but can deliver that performance over an extended life expectancy of the product. Key factors include high-performance products, optimized manufacturing techniques with minimal touchpoints, and proper field installation for long-term, sustainable building design.
Longevity is critical to holistic sustainability. Restoring a failed or malfunctioning component of the building envelope fundamentally involves more raw materials and manpower associated with manufacturing and installing the replacement product. This is a detriment to the overarching sustainability effort—a failed product is simply a waste of resources, and we need to be doing what we can to avoid such a situation.
There’s the economic side to this, too. No architect or developer wants a critical part of their project to fail prematurely, nor the warranty and replacement costs that would come with it. None of which is to mention the reputation damage that comes with a failure.
Seeking and specifying reliable, proven, high-performance glass and glazing products is the answer to each of these problems. Achieving new heights in sustainability relies upon it, and it behooves all stakeholders in our industry to continue collaborating to find the most suitable solutions.