A New Era for Everyday Maintenance
Modern equipment requires new tasks and techniques to remain optimally functional. Are your maintenance teams up to the task?
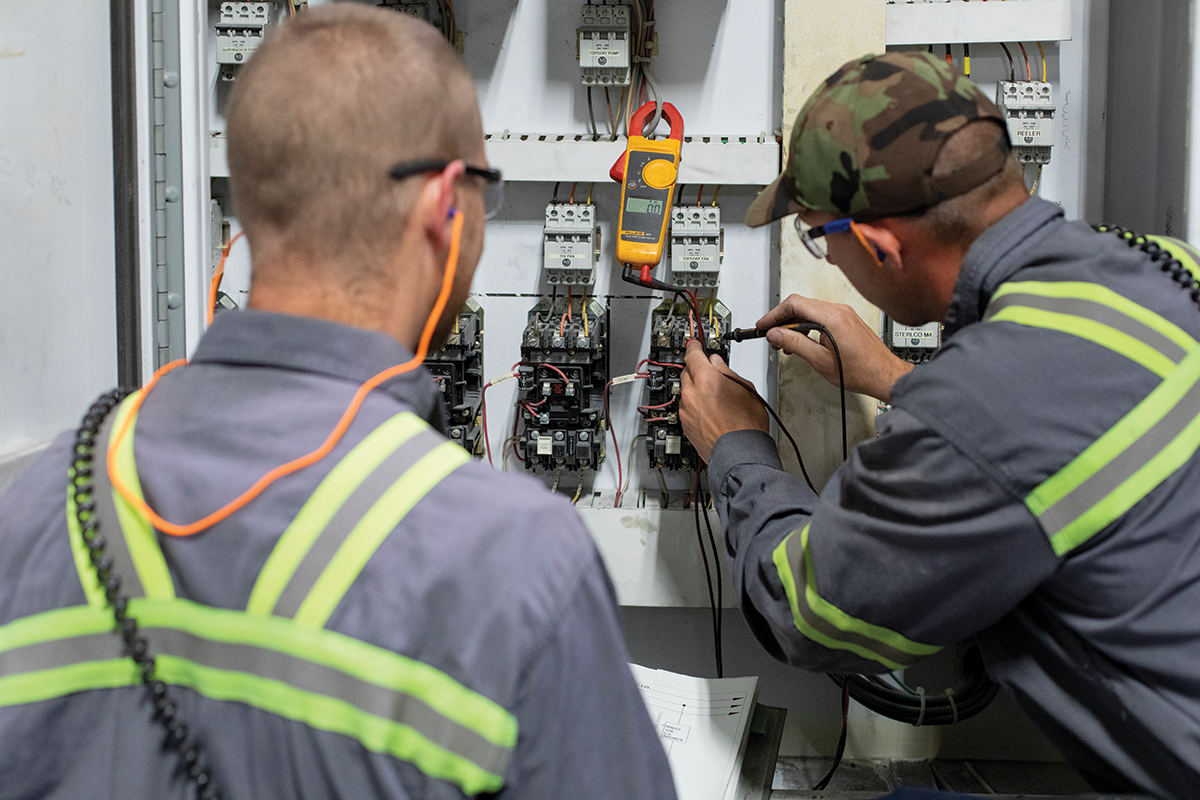
Above: Insulating glass system maintenance at Quanex plant in Cambridge, Ohio. Photo courtesy of Quanex.
The Bottom Line: Maintaining an efficient automated commercial glass manufacturing floor requires proper equipment training, versatile maintenance teams skilled in both modern and fundamental techniques, and consistent preventive maintenance to ensure smooth operations and maximize equipment longevity.
An ideal version of the modern commercial glass manufacturing floor is a marvel of cutting-edge equipment and process optimization. Massive panes move seamlessly down the line, where spacer systems are applied accurately and consistently. Raw materials are always ready. Finished products are barcoded and efficiently loaded onto shipping trucks in strategic order and sent off to satisfied customers.
None of this happens by accident, of course. Automated lines aren’t magic; this kind of synchrony only works after careful preparation prior to installing new equipment, proper training for line workers, and regular and consistent maintenance.
About that last part. Automated equipment requires different maintenance needs than more traditional manual machinery, which means maintenance teams must evolve their skill sets to stay ahead. Otherwise, the ideal modern manufacturing line comes grinding to a costly halt. And your investment in cutting-edge equipment may not pay off in the ways you expected.
To ensure your maintenance teams are up to the task of keeping your new equipment in good working condition, here are a few points to consider.
Getting in tune
Where conventional manufacturing maintenance tasks were once accomplished by “jack-of-all-trades” technicians, modern equipment—in the commercial glass space and elsewhere—is increasingly specialized and specific.
This means a few things for your maintenance crews. The first is that proper training is required to get and stay up to speed on these new needs. You should work closely with your equipment suppliers not just to get the machines online, but also to understand ongoing maintenance tasks that will keep them running smoothly over the long term. Importantly, your maintenance teams will need to keep an open mind about new ways of doing things—today’s commercial glass maintenance technicians need to be versatile, adaptable and capable of applying new strategies to maximize equipment performance and life.
Elsewhere, you should investigate simplified installation for product components. For example, metal and other rigid spacer bar systems require pre-assembly of multiple components to complete the unit’s edge seal. These components include the spacer itself, corner keys and desiccant. Comparatively, flexible spacer systems with integrated desiccant require no such pre-assembly processes, leading to simpler and more efficient fabrication.
When investing in new equipment, component selection is critical. It’s worth doing your due diligence, as some options are more suitable to modern equipment than others.
Don’t forget the fundamentals
While maintaining automated equipment requires more sophisticated skill sets, some maintenance strategies never go out of style.
For example, the preventive maintenance program is a necessity no matter the age of your machines. These daily, weekly, monthly and annual tasks can go a long way toward optimizing processes when put into practice on manufacturing floors. Ensuring your teams perform preventive maintenance tasks consistently and on schedule is key to keep machines in top condition. A preventive maintenance checklist might include things as simple as greasing bearings on a machine or as complex as dismantling the glass washing station for a thorough evaluation and cleaning. These tasks must follow a regular schedule to maintain preventive maintenance program effectiveness.
During busier times of the year, when production is running at full steam to satisfy orders, it can be easy for maintenance practices to fall by the wayside. Preventive maintenance requires making time for these activities, no matter how many orders are coming in. Here, production and maintenance teams should communicate and operate in sync. That might involve collaboration on timing, schedules and other accommodations, as necessary.
No production team is successful without the maintenance team, and no maintenance team is successful without the production team. Reliable equipment that works safely and consistently enables production of high-quality products for your customers. Simultaneously, consistent, high-quality production enables maintenance teams to focus on proactive—rather than reactive—tasks that keep your entire operation running smoothly. Plant managers and shift supervisors should work to encourage this mindset.
Getting the most from your investment in automation depends upon your commitment to good maintenance practices. In our new era of commercial glass fabrication, it can make all the difference.