Q + A with Viprotron North America | Revolutionizing Glass Quality
Fabrication technology is ever-evolving, and game-changing advances offer up new ways of addressing inspection and quality control
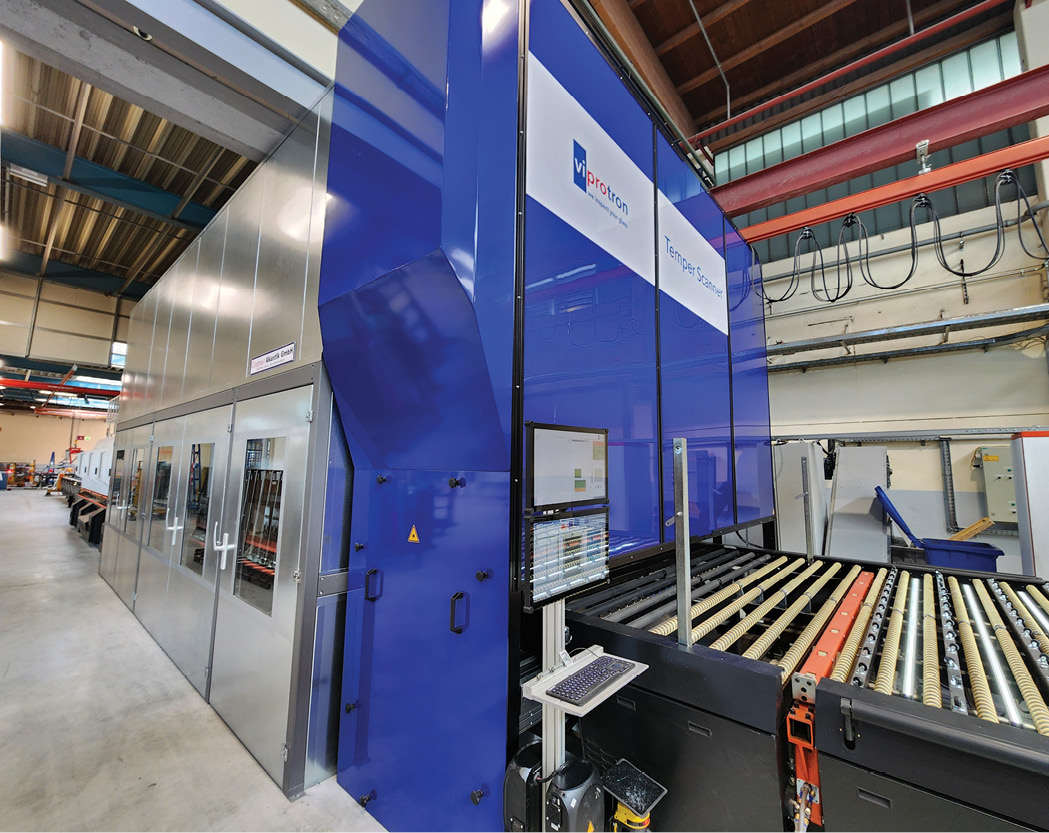
Above: The Temper Scanner 5D with True Edge™ technology by Viprotron, in use at Vandaglas Eckelt in Austria.
Quality control remains a crucial step in the manufacturing of architectural flat glass. The complex production of float glass can introduce structural defects in every sheet. And architects using increasingly larger lites of glass in commercial construction require tempering for durability and safety.
To ensure high-quality products, glass manufacturers employ various methods to inspect and test their products, including visual inspection and chemical analysis. As automation continues to be embraced by manufacturers, advanced technologies that streamline the process of quality control and checkpoints are gaining attention, and traction.
Glass Magazine sat down with Viprotron North America President Ric Schmidt and Customer Experience Director Jakub Kowalczyk to discuss why advanced scanning technology is needed industry-wide, the specific technology of tempering scanners and its impact on the demand for quality, the increasing use of AI in the quality control process, and why glass manufacturers should invest in advanced scanning technology.
Glass Magazine: Why is advanced scanning technology needed industry-wide in the glass industry?
Ric Schmidt: Glass quality expectations keep growing every year. Glass that has minimal defects and distortion keeps customers satisfied, protects their reputation and minimizes financial losses. Our goal is to help customers maintain quality—from the initial piece of jumbo glass to the finished product—ensuring no value is added to flawed or damaged pieces. Ultimately, we aim to save customers money and time and improve their products.
GM: How do you see the glass industry evolving in terms of automation and data-driven quality control?
RS: In today’s world, manufacturing is data-driven in basically every aspect. From raw materials coming in, to finished products shipping out, data allows for better analysis and for instant reaction to what is happening on the shop floor. The companies that collect the right data and then put it to use will make more money and increase their quality in any industry.
GM: With the current labor challenges in the glass industry, how does advanced scanning technology impact the demand for quality?
RS: There’s a problem with hiring enough people, and a lack of adequate talent, to do the right work. Many years ago, people were processing glass by hand, like making IGs and visually inspecting glass for flaws, and we didn’t have machines doing it. There are still a few shops doing things by hand, but they’re hard to find. So, the talent you have on the floor needs to be doing value-added things to make good products for your customers. A relatively inexpensive but high-value scanner allows you to be in the quality game, relieving someone so they can go do something else. It’s not a job killer. It helps keep your talent where it needs to be, instead of doing things that we can do for you. And it helps you make a better product.
GM: What specific technology in Viprotron’s tempering scanner sets it apart from others in the market?
RS: Viprotron uses digital line scanning technology that analyzes glass one pixel line at a time, from edge to edge, for the entire length/width of the glass. We use a patented light pattern to precisely measure the distortion caused by the tempering process, which produces exceptional data. We also offer five different detection channels on our tempering scanner; it’s the only piece of equipment in the marketplace that can do that after a furnace.
The five channels highlight most of what we do when we scan glass. We check distortion, anisotropy or haze and streaks on the tempering side, and the glass quality itself, including the coatings for any scratches, pinholes, etc.
Jakub Kowalczyk: We’re about the excellence of the data. Whoever can get and use the best data is going to end up better off than the company that doesn’t. Today, furnace operators use our data to adjust the settings to reduce the flaws inherent in the tempering process. The vision for tomorrow is that our scanner talks directly to the furnace, and maybe nobody’s involved. And the only way that can happen is if the scanner is providing consistently accurate data. It’s about providing precise data that the operator can use to produce high-quality tempered glass. Excellent data leads to excellent results.
GM: What role does AI play in your scanning technology, and how do you see it evolving in the future?
JK: Industries change, and if you have the most accurate data, then you can perhaps use that data to do better than your competitor. With five channels on the tempering line, we collect the most accurate data and much more of it. But you need a mechanism to analyze it and apply it correctly.
GM: What challenges do smaller, family-owned glass companies face when investing in high-tech scanners?
RS: It’s a big commitment from an investment standpoint. Individually owned businesses are not going away anytime soon. It remains one of the few industries where individual, family-owned businesses continue to thrive. But the focus on quality is not only affecting the larger corporations, good quality is going to trickle down to everybody. So, they do need to consider it.
We offer a very inexpensive solution for people to get started with our ECO scanner. It’s one channel, easy to set up and the customer can do it himself. We designed it specifically to be DIY—send them the box with the instructions, they set it up and can begin checking for ASTM standard defects.
GM: What advice would you give to a glass company considering its first investment in a scanner?
RS: Everybody wants a scanner, but you’ve got to do something with it. Don’t just buy it, place it somewhere and walk away. Make sure you do something with the information you’re getting so that you’re actually analyzing when flaws are happening, what flaws keep happening and what needs to be fixed upstream. That’s using a scanner to benefit your customer and your bottom line. You should be using it to the best of its ability to help make better glass and better decisions. That’s the point.