Q+A with Quanex | Warm Edge Revolutionizes Glass Fabrication
Warm-edge spacer technology boosts efficiency in modern automated glass fabrication
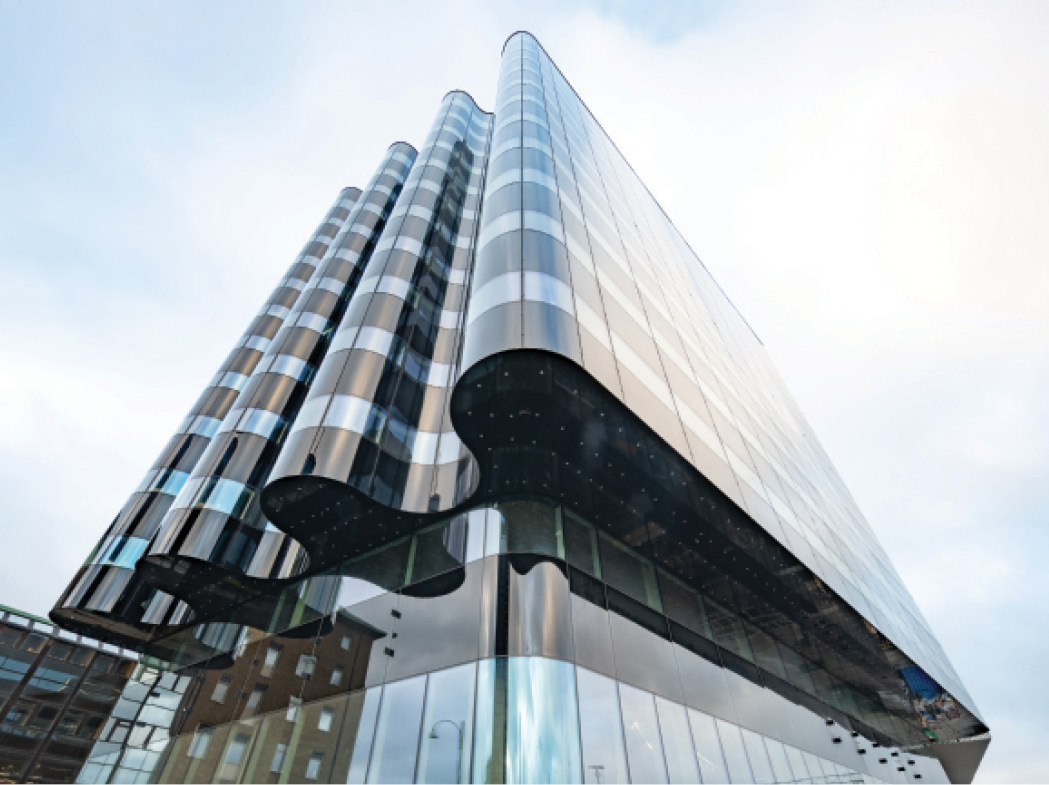
Above: The 13-story Våghuset Business Centre in Gothenburg, Sweden, features an undulating curved glass façade. Flexible warm-edge spacers by Quanex were used in the project. Photo courtesy Quanex.
Warm-edge spacers have been around for generations—as far back as 1865, in fact—but the technology gained traction in the 1980s as a response to concerns over energy efficiency and condensation in insulating glass units. In recent years, warm edge technology has started to thrive once more as manufacturers look to reduce heat transfer and improve insulation properties in windows and glass units to keep pace with the growing demand of sustainable building coupled with increasingly stringent energy-efficiency codes and standards.
Mike Moran, global market director, and Joe Erb, national account manager, Quanex, sat down with Glass Magazine to discuss the efficiency and performance gains of warm-edge spacer technology in commercial insulating glass, and how it lends itself to modern, consistent and efficient manufacturing strategies.
Glass Magazine: Let’s start by defining what warm-edge spacer technology is.
Joe Erb: Spacer technologies have progressed over the years, but I think it’s important to note that not all spacers or warm-edge spacers are the same. It’s very broad and the industry continues to wrestle with defining warm edge. I would generally describe warm edge as an insulating glass spacer system in which the spacer provides improved thermal performance over traditional conductive aluminum or metal spacers.
Mike Moran: Yes, warm edge covers a vast number of products and technology. There is a large difference between one warm edge technology and another. In terms of thermal properties, there’s a massive spread. For example, stainless steel compared to foam silicone, there’s five or six times more improvement in the calculated thermal property and thermal efficiency. And then if you compare it to aluminum, it’s more like a factor of 1,000 times lower thermal conductivity.
GM: How does warm edge technology improve the thermal performance of IGUs?
JE: Flexible warm edge offers significant improvements in IGU thermal performance by reducing heat flow through the edge of the glass. But there’s so much more available to the end user and manufacturer when selecting the right warm edge than just the thermal benefit. Thermal is obviously extremely important, but a good flexible warm edge solution covers a variety of other performance benefits such as improved quality, durability, condensation resistance, sightline aesthetics, as well as reduced touch points, acoustics and more.
GM: How can it integrate with existing automated equipment and processes?
MM: A big advantage is that you can automate and end up with a more efficient fabrication line at the end of it, both in consistency of quality and in capacity and output. Technical service support is essential to [installing] an automated line. When you’re changing from non-warm edge to a flexible warm edge, you do have to change your production methods a bit, and you do need some assistance with that.
GM: What challenges could fabricators face when transitioning?
JE: I think one involves the unique approach to assembling IG. With rigid spacer bar, the fabricator must assemble many components offline into a spacer bar frame (spacer bar, joiner keys, primary sealant, desiccant, etc.), which is then applied to the glass. It’s an assembly process the person on the line must remember to do properly and in the right order. With flexible warm edge technology, that mentality must shift because there is no spacer frame assembly process required by the fabricator. Flexible spacers are provided by the supplier on continuous reels and applied directly to the glass via robotic applicators on demand.
The other consideration is for production personnel to change the way they look at and approach manufacturing. Automation streamlines that process, reducing up to 60% in labor, and while it’s not challenging it requires a change in mindset on the approach. And once fabricators get used to it, it becomes a much more simplified approach to manufacturing IG.
GM: How does Quanex assist fabricators in adopting or implementing the technology?
JE: This is a crucial interactive component of our company. Teaching [customers] best practices for using our products is an essential part of what the Quanex Technical Services team does.
When new equipment comes in, we work with our customers and the equipment supplier to get the equipment up and running properly. From there, we make sure they’re trained in best practices for using our spacer product to make a truly durable and sustainable IGU. We follow up periodically with quality reviews and audits.
GM: How does adoption affect the overall production cost for commercial fabricators?
JE: Warm-edge spacer tends to cost more because you’re adding polymers and high-performance materials compared to traditional metal spacers. The flexible warm-edge spacer production process can reduce labor requirements by 60% compared to the rigid warm edge or metal spacer production process, making it a very cost-competitive warm edge solution that brings a bigger value proposition to the table. It’s not just about warm edge, it’s about the entire package the spacer system offers.
GM: How can fabricators ensure consistent quality by implementing warm edge in their production?
JE: In manufacturing, if we can reduce the number of human touch points in the IG production process, we reduce the potential for errors that lead to quality issues, remakes or returns. A flexible warm-edge spacer IG line only requires two or three people where a rigid spacer line may require eight or nine. That means six or seven less touchpoints/human interactions with glass and components for improved consistency and quality.
GM: With warm edge technology evolving, what should fabricators be aware of?
JE: Warm-edge spacer designs have been in the market for more than 35 years and are increasingly being specified to help improve thermal efficiency of façades and improve efficiencies in production. There are many warm edge options for a fabricator to choose from.
As fabricators look to invest in new IG lines to meet these requirements and address ongoing labor challenges, they’ll find flexible warm edge solutions offer the best return on investment in today’s market. It’s important to do your research and work with reputable suppliers with a strong history in the spacer market. At the end of the day, awareness of what true warm edge can do for the market and what the right warm edge can do in manufacturing elevates the industry.