Strategies for Glass Curtain Wall Installations
Efficient installation can help glazing subcontractors pin “big ticket” costs and optimize the process
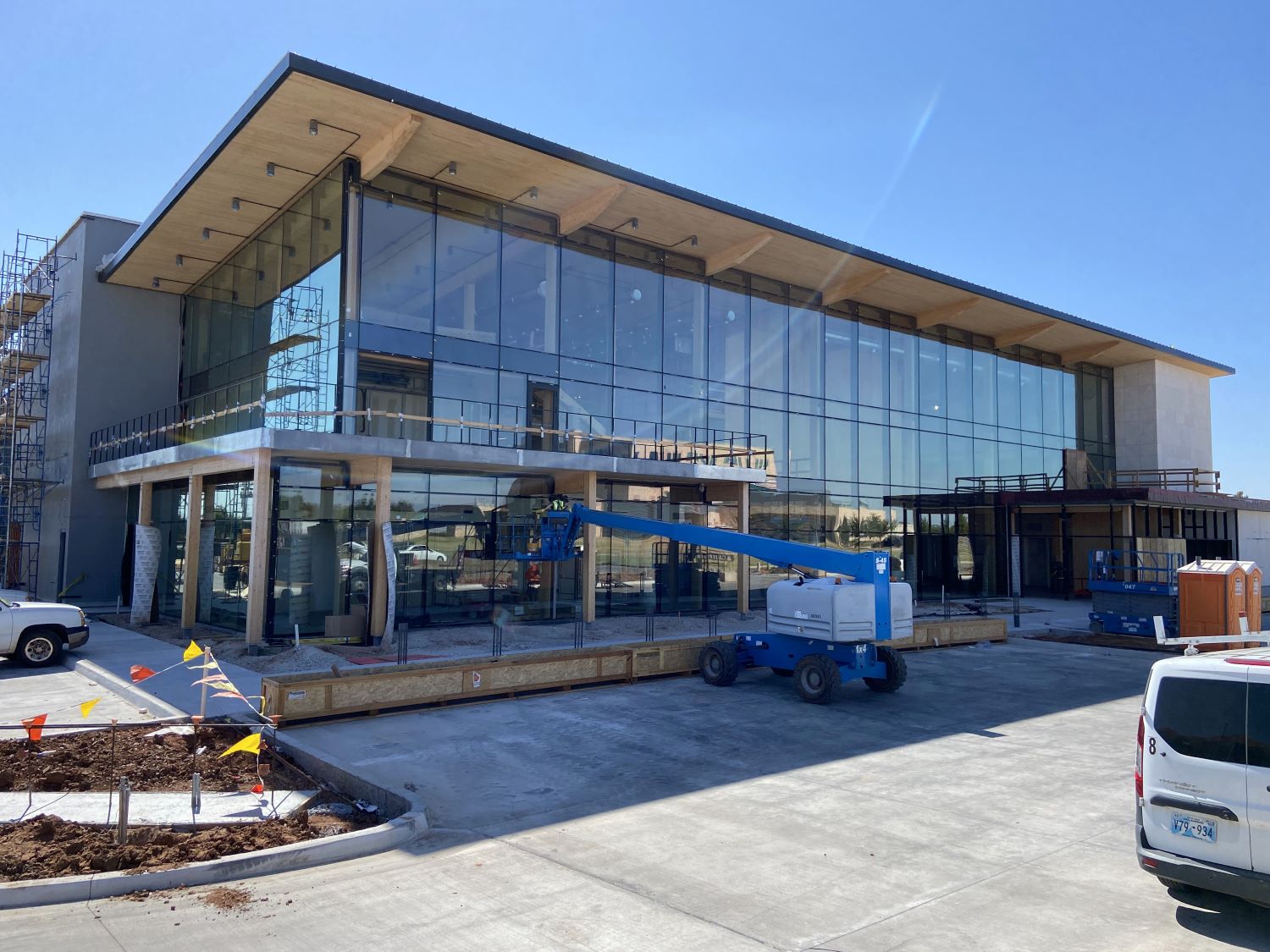
Above: Well-planned glazing installation can help with the quality of work delivered, project timelines and costs. Photo courtesy of TGP.
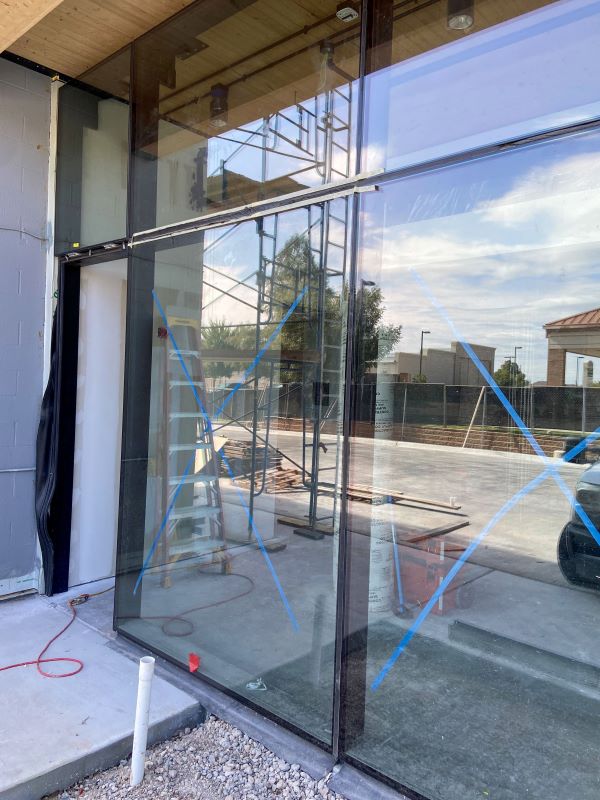
Curtain walls present unique challenges and opportunities to glazing subcontractors compared to other typologies, such as storefronts or punched windows. These systems have been around for a long time and are likely to stay. Being able to install them better, cheaper and faster can help glazing subcontractors find where the “big ticket” costs and schedule items are and optimize the process.
Pre-installation considerations
Stick-built curtain wall systems are fabricated before they’re shipped and assembled on-site. Whereas, in unitized wall systems, complete wall panels, usually one module wide (center-to-center of mullions being the module width) by one-story tall, are factory assembled and glazed, then shipped to the site. Generally, they are quicker to install than stick systems. Both systems require a lay-down area, but crating materials in smaller bundles or stackable skids might save on the required floor area.
For stick systems, any overlap between the deliveries of fabricated framing material and glass might increase the required floor area and the risk of damaging glass lites. The whole process of lifting the lites or units requires special equipment for heavy lifting. However, as unitized systems are pre-assembled, the time needed to load floors with pre-assembled units is likely different than that required for stick systems. Usually, the floor space is more quickly turned back to the general contractor.
After the frames are erected and glazed, follow-on activities complete the installation in stick-built systems, such as adding insulation, safing and smoke seals, and any necessary interior trim. The glazing subs must also carefully clear dunnage from floors in stick-built systems. The skids that carry the unitized panels to the site are often returned to the shop for use in future deliveries, negating the need to dispose of them. Planning such details can be critical to the construction schedule and budgets.
Successful installation tips
There are many aspects to consider for successful glazing installations. One of them is sealant strategies. Glazing teams may need to pay more attention to appropriately sealing stick wall assemblies in the field. In contrast, this aspect is often handled during shop assembly in unitized walls. The field seals between unitized panels are repeatable and fairly easy to accomplish.
Another is the glass size. With larger lites coming to the fore in both stick-built and unitized systems, there is less material to procure, fabricate and install. But for glazing teams, this requires increased caution in handling and installing larger lites. Additionally, sourcing the right equipment to handle these can be crucial to safe and timely installations.
Timelines for deliverables
While equipment and storage are important to ensure timely deliverables, glazing subcontractors can evaluate the commonalities between the two systems to streamline installation time and costs. One is how the system is anchored to the building. Simplifying the anchoring to the greatest extent possible can greatly impact field installation costs. Most unitized wall systems have anchor systems with built-in adjustability for in/out, left/right and up/down setting tolerances within acceptable limits, generally, +/-1 inch in any direction.
The stick-built system’s anchoring mechanism tends to be simpler, consisting of anchor clips bolted through vertical mullions and connected to embeds (in concrete structures) or welded to structures (in steel-framed buildings). Their installation can be further simplified if the unitized wall’s anchoring concepts could be applied to them.
In all of these, planning is key. Sitting with the general contractor, ideally when the proposal is submitted, working out the time and delivery of materials to the site, regardless of the system, can lower costs and simplify site logistics for a glazing sub. Discussing anchor tolerances and how much the general contractor will control the edge of the floor slab is also a worthwhile effort.
But looking internally within one’s operations is well worth the time, effort and expense if a better, cheaper and faster way can be found. In the past, I’ve seen glazing subcontractors on new projects sit down with their project managers, field supervisory personnel, material suppliers, and engineering resources to carefully examine every phase of the planned installation. Everyone has an equal say with the added benefit of immediate feedback and understanding within the team of the “why are we doing that” aspect of the installation.