World of Glass 2023 Report
North American float glass manufacturers explore partnerships with solar panel producers and stay ahead of the curve with low-carbon products
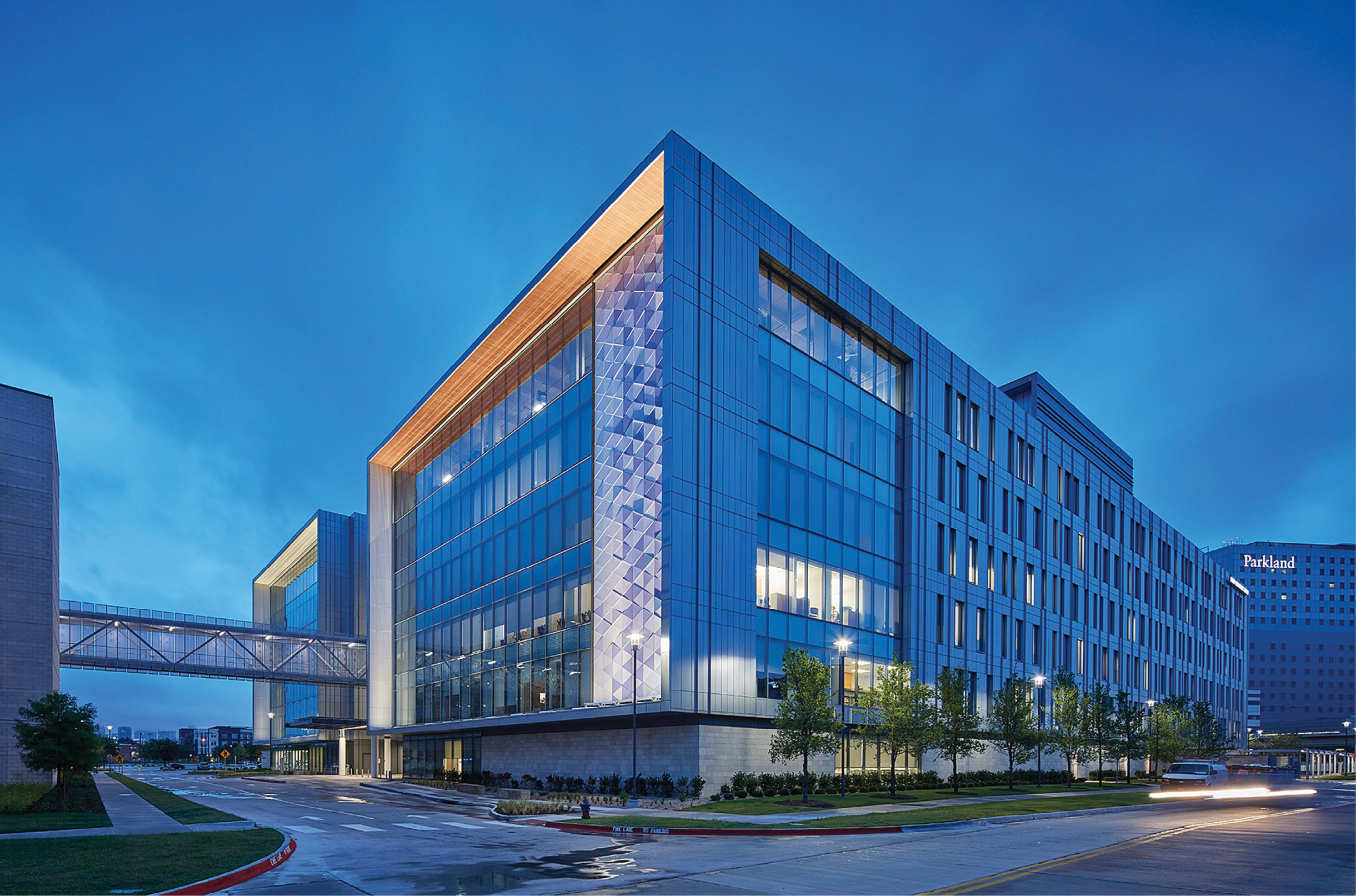
Above: The Parkland Moody Outpatient Center, a LEED Gold-certified health care facility in Dallas Texas, features natural daylighting thanks to Vitro Architectural Glass’s Solarban 90 Acuity glass. HK Architects specified the product for its transparency, color neutrality, solar control and visual light transmittance. Partners included fabricator Hartung, and glazier IWR North America. Photo by Tom Harris.
What a difference a year can make. That was true of the North American, and indeed global, float glass industry in 2023. As inflation continues to depress commercial and residential building, a new segment of the float glass industry is emerging: glass for solar panel production. In this uncertain environment, North American producers are having to set their sights both short-term and long-term; meeting customer demands for increasingly stringent energy performance while improving and updating manufacturing processes for sustained pushes toward industry decarbonization.
Download the World of Glass Database
The World of Glass database presents sortable information for dozens of float glass manufacturers operating more than 230 plant locations with more than 450 float glass lines. The database includes company and location details for each plant.
The database is available for purchase in the National Glass Assoc. store and is free to NGA members.
Solar panel production may transform supply in North America
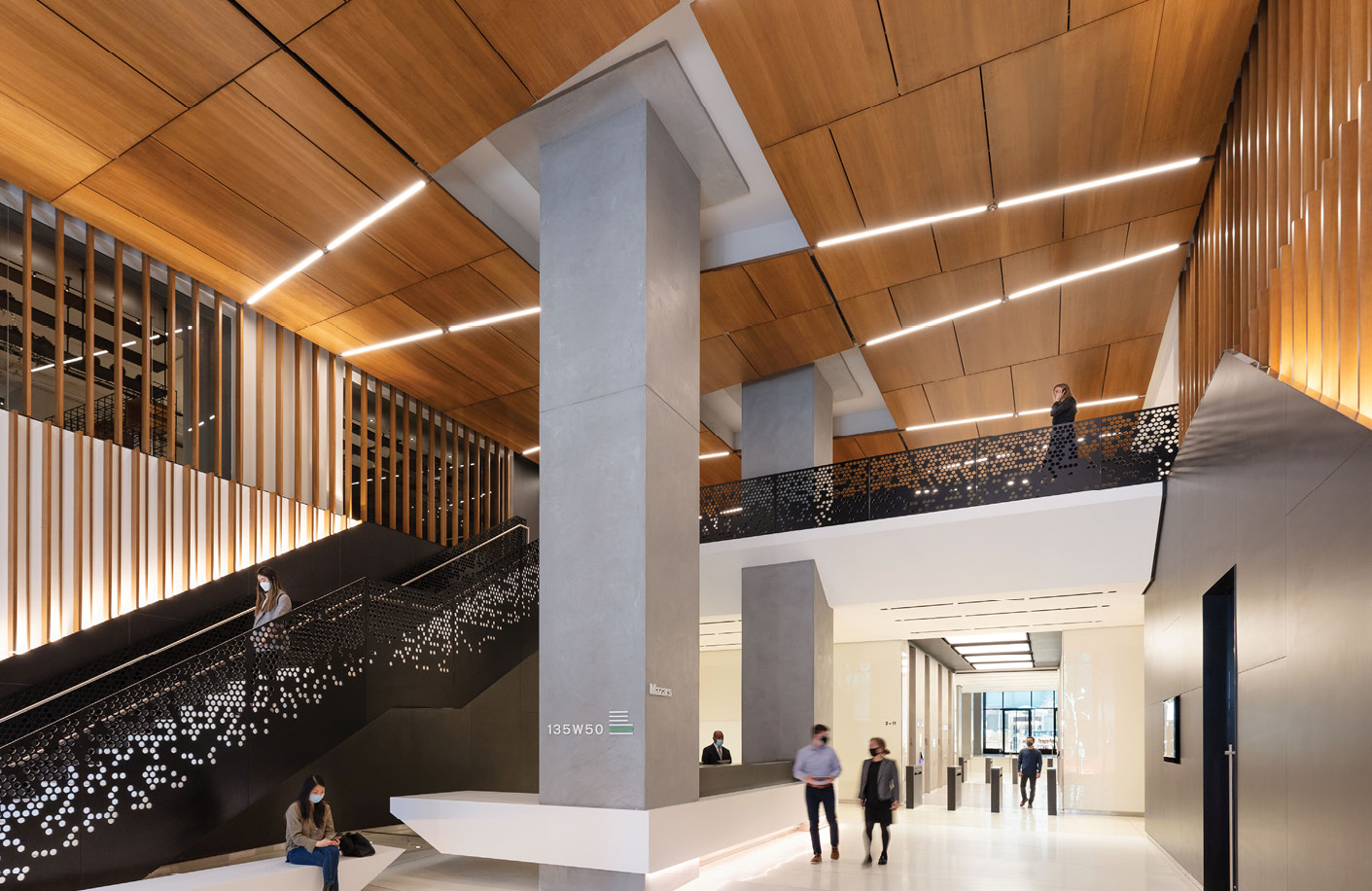
While the float glass supply in 2022 was tight, that changed in 2023 due to economic slowdown, says Stephen Weidner, president and head of architectural glass North America and solar products, NSG Group. Unprecedented inflation and interest rates have depressed both the commercial and residential markets in North America, and the “domino effect” of the pandemic continues to affect commercial building, including office and retail construction and even institutional builds, he says.
While the dip in demand might have led to overcapacity, says Weidner, the expansion of glass supply to solar panel, or photovoltaic, production has balanced this out. “This growth in the solar [panel market] has absorbed a lot of this under-utilized capacity that we would have historically seen in the market from all these negative impacts,” he says.
Glass for solar panel production grows to 5% of the market
Weidner says glass for solar panels is now a significant sector of the raw glass market, joining the commercial/architectural, residential and automotive segments. To demonstrate the sector’s rapid growth, demand for glass from the solar panel market has risen from 0% five years ago to 5% of the market in 2023, says Weidner. About three North American float lines are now fully dedicated to the segment, he says, and that’s just the beginning. “If you look at next year, it's going to be four lines, and the year after that will be five or six lines.”
Both NSG Group and Vitro Architectural Glass supply First Solar, a solar panel manufacturer. NSG’s Luckey, Ohio, plant supplies First Solar in the U.S., and the company announced in November 2023 that a float line at its Rossford, Ohio, plant will install online coating capacity and will start shipping transparent conductive oxide glass for solar panel manufacture in the first quarter of 2025. The company has also increased glass supply to the sector globally; it converted a float line at its factory in Johor, Bahur, Malaysia, to produce TCO glass. “NSG is also considering expanding further capacity for solar energy glass in the U.S., to ensure it meets solar glass demand by First Solar,” say officials in the announcement.
Vitro’s partnership with the company accelerated in 2023; they announced their first contract in April and another in October of that year. Vitro is rebuilding its second line at its Meadville, Pennsylvania, plant to supply the contract; the float line had been idled due to low capacity and the prohibitive cost of rebuilding it at the start of the pandemic.
Following the company’s second contract with First Solar, Vitro announced that it would idle line 1 at its Carlisle, Pennsylvania, plant in order to reconfigure it to produce glass for solar panels. Line 2 at Carlisle will continue to manufacture glass for commercial and residential applications. Overall, the company is investing about $180 million to refurbish the Meadville and Carlisle plants to produce glass for First Solar, according to officials.
“The agreement further strengthens our supply chain, not only in the U.S. but also in North America,” says Paul Bush, vice president, technical services, sustainability and government affairs, Vitro Architectural Glass. “Our Meadville plant already has the necessary raw materials, and its strategic location is well-suited to accommodate First Solar’s production.”
Solar panel producers expand in the North American market
First Solar itself is also expanding. In September 2023, the company broke ground on a new facility in Louisiana, with plans for further expansion in Alabama and Ohio. The Inflation Reduction Act has incentivized the production of PV panels, and several companies have announced new locations in the North American market, including Canada-based Heliene; Meyer Burger Technology AC, based in Switzerland; Italian energy company Enel; and Vikram Solar, an India-based solar module producer.
Canadian Premium Sand, which in 2021 announced plans to build a new float plant, continues to develop manufacturing capacity for a patterned solar glass facility to be located in Selkirk, Manitoba, Canada, slated to be operational in 2025. An update on the project in August 2023 noted that the expansion of solar panel manufacturers in the North American market represented “an additional 29 [gigawatts] of potential incremental demand for patterned solar glass and brings [CPS’s] current estimate of market demand to over 100 GW by 2027.”
Glass supply remains a headwind for future growth of solar panel production
Other than Canadian Premium Sand, the new market is unlikely to be supplied by new U.S. float plants soon, says Cardinal Corp.’s Bowie Neumayer, vice president of sales and marketing. “Economics make it very hard to build a float plant today. The cost is very hard to justify,” he says. Inflation has even further dampened float producers’ ability to build new lines, says NSG’s Weidner. “The inflation we’ve seen in the last couple years has impacted the cost of building a new line, and to repair existing ones. That’s impacting the industry in general, and not just in North America,” he says.
Assuming no new significant capacity in North America, the increased supply of raw glass for solar panel production may pinch supply for other sectors, says Weidner. While he hopes for the rebound of the commercial and residential markets, once they do return, it will likely mean a very tight glass market. “I do see that the demand will outstrip North American supply at some point,” he says, possibly a year to three years in the future, a development that may result in increased overseas imports.
Global challenges may imperil industry growth around the world
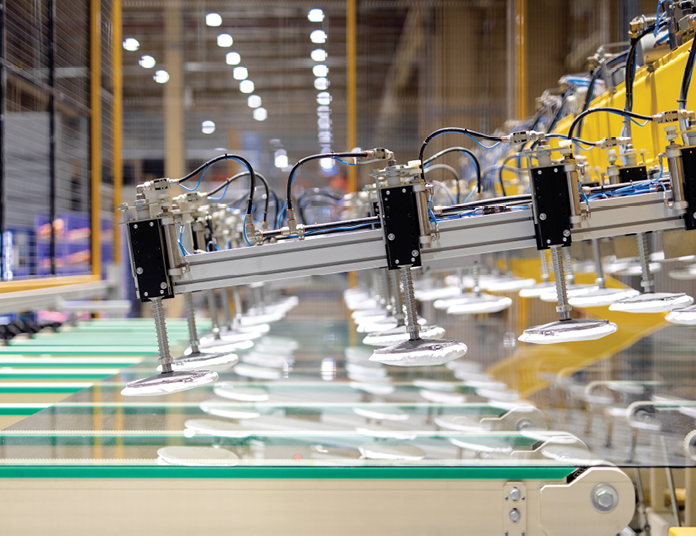
This last year continued to see major global challenges. As of this writing, a new conflict in the Middle East has compounded global tensions already running high due to the war in Ukraine. In June 2023, NSG Group disposed of its joint venture in Russia, and Guardian Glass sold its two Russian float facilities the previous summer.
Ongoing conflicts have the potential to disrupt the glass supply for North America. Although about 97% of North America’s leading fabricators source glass from North America, according to Glass Magazine’s 2023 Top Glass Fabricators report, 29% also source glass from Europe and 24% from Asia.
Wassim Khalil, commercial manager, Sphinx Glass, one of three float producers based in Egypt, says the regional float glass market is robust. “The glass market is growing, and it will definitely grow more because of the growing population in Egypt, Africa and the Middle East. There’s a demand for glass there.”
That growth will depend on regional stability, he says. “When I say stability, I mean economic stability and political stability in our region, so we can invest more in the coming five years to meet the demands of the market,” he says. “If there is no stability, I doubt that any one of us will put more money into that sector in the industry.”
Representatives at Xinyi, a major float producer headquartered in Asia, say the Asian market is also seeing “robust growth.” “Around 80% of the world's production capacity is concentrated in Asia, underscoring the region's significant market influence,” says Harold Wang, head of the international sales division, Xinyi Float Glass.
The company is currently opening a new float plant in Indonesia, scheduled to be operational within the next year, says Wang, and is looking to expand further. “In an effort for global business expansion, Xinyi remains open to partnerships with reputable local partners.”
Float producers continue to lower embodied carbon through sustainable manufacturing
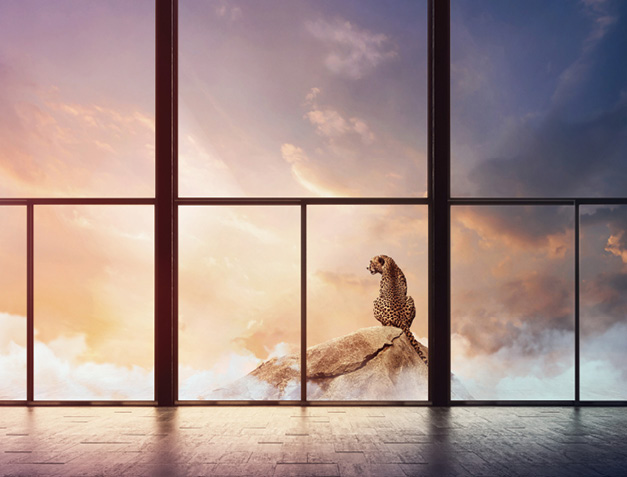
In 2023, NSG Group became the latest float glass producer to offer a low-carbon, flat glass product, Pilkington Mirai. Mirai represents a 50% reduction in embodied carbon compared to standard float glass, according to the company, which was accomplished using biofuel. The range joins low-carbon offerings, including Planibel Clearlite by AGC and Oraé by Saint-Gobain.
Using alternative fuels to power float glass production requires significant technical consideration and is a complex process, says NSG’s Weidner. “The availability of some of these other sustainable fuel sources is rather limited because the market hasn't created need from a demand perspective,” he says. Beyond availability and cost, the company also has to consider the impact of different fuels on production equipment, he says.
Guardian explores furnace alternatives towards sustainability
Guardian Glass is exploring power alternatives like electric melting, or “boosting,” through a partnership with Glass Futures, a global non-profit research and technology organization that aids companies in decarbonization by encouraging knowledge-sharing across the supply chain. The partners have created a pilot float line with a furnace capable of using electric melting to provide up to 60% of the energy required to melt glass, says Rick Zoulek, executive vice president, Americas, Guardian Glass.
“The challenge is for us to transfer these projects from the concept stage to full production without disrupting our operations,” says Zoulek. “The Glass Futures pilot line will provide an opportunity to try out some of our concepts on a furnace so we can de-risk the implementation of new technologies onto our float furnaces.”
Guardian also recently completed a successful cold tank repair of its furnace at its Bascharage, Luxembourg, facility. The furnace is now the most energy-efficient the company has, Zoulek says, consuming 25% less natural gas when compared to traditional furnace methods.
Floaters communicate material transparency through EPDs
Embodied carbon and global warming potential continue to be of interest to architects. Environmental Product Declarations, or EPDs, remain one of the main ways companies can express material transparency and global warming potential to the design community. “EPDs are technically voluntary, but they’re really a necessity,” says Alan Kinder, director, commercial segment, Guardian Glass. “You can’t walk into an architect’s office without it.”
Guardian plans to release an updated North American flat glass EPD in early 2024, with a cradle-to-gate embodied carbon value that will meet the top 20% limit in the General Service Administration’s Low Embodied Carbon Material Standard.
Vitro released updated EPDs for flat and fabricated glass in June 2023. The updated glasses now contain 6% lower embodied carbon than the National Glass Association’s industry-standard figure. Vitro officials say more efficient use of batch material, furnace efficiency and oxy-fuel technology all aided in the carbon emission reduction. Oxy-fuel can reduce energy consumption in glass melting furnaces by as much as 20% and cut greenhouse gas emissions in half, say officials. The company also offers sustainability resources on its website, including a Cradle to Cradle Certified Material Health Certificate, a LEED Recycled Content Letter, Material Safety Data Sheets and a Living Building Challenge Red List of Materials.