World of Glass 2025 Report
The Decarbonization Equation
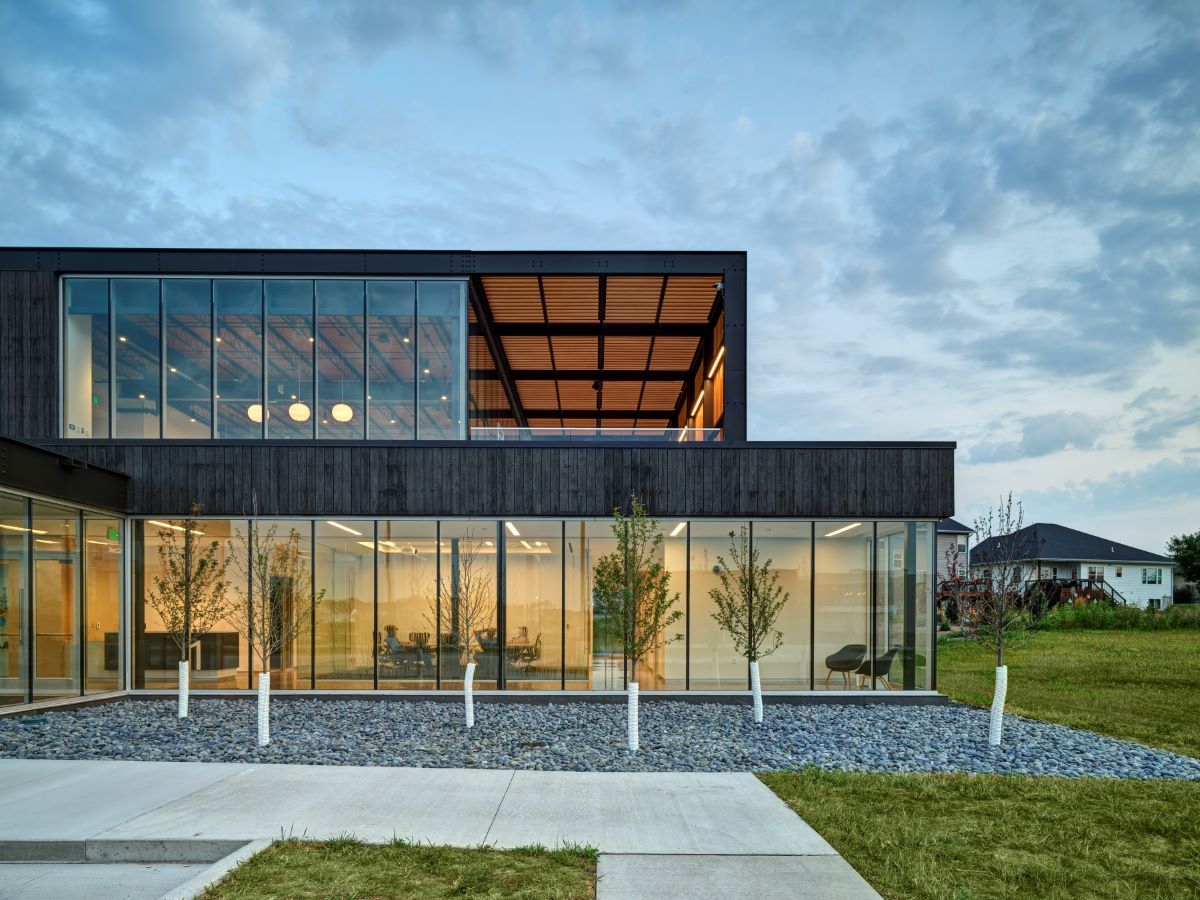
With contributions from Norah Dick and Rachel Vitello
Above: Buildings account for approximately 40% of the total energy use in the U.S. Improving facade performance can reduce building energy consumption. Pictured is the Marion Fire Station in Marion, Iowa, designed by OPN Architects, with low-emissivity glass from Vitro to maximize daylighting and thermal performance. Photo courtesy of Vitro.
The glass industry has witnessed several step changes in manufacturing in the last 100 years—the global adoption of the float glass process following its invention in 1952; the standardized use of insulating glass following the energy crisis of the 1970s; and the introduction of glass coatings (beginning with low-emissivity) in the 1980s. But what comes next? What is the next step forward for flat glass? These were the questions Glass Magazine posed to industry leaders during the global glass event glasstec 2024, held Oct. 22-25,2024, in Düsseldorf, Germany, where two sustainability themes emerged: decarbonization and circularity.
How can the global glass industry, in all segments, address the need to reduce embodied and operational carbon? The answer, per glass manufacturing leaders, requires improvements in three areas: manufacturing, recycling and reuse, and installed product performance. And it requires the participation and investment of companies across the industry.
“We need to take responsibility,” says Sisecam CEO Görkem Elverici. “We believe that in order to envision, design, discover, innovate and implement the solutions of the future, we must move forward together. In our rapidly changing world, industries that rely on traditional/conventional methods must adapt to this transformation.”
Download NGA's World of Glass Database
NGA recently relaunched its World of Glass Map resource on glass.org. The searchable map features information about global flat glass manufacturing locations, North American glass fabrication capabilities, and recycling locations for flat glass. Recycling location research is underway.
The updated for-purchase World of Glass Database includes worldwide location data for over 200 global float manufacturers as well as North American fabricators. Available in the National Glass Assoc. store, the database is free to NGA members.
Decarbonizing manufacturing
Glass manufacturing is an energy-intensive business. An estimated 78% of embodied carbon in an insulating glass unit comes from the glass manufacturing process itself, according to the Efficient Windows Collaborative. Reducing carbon during this process can have the biggest impact on the industry’s overall carbon emissions.
Reducing embodied carbon has become a key focus of glass manufacturers, with companies such as NSG Group aiming for a 30% reduction in emissions by 2030 and carbon neutrality by 2050. In pursuit of these efforts, NSG Group introduced Pilkington Mirai in 2023, which is manufactured using a combination of alternative fuel, high recycled glass content and 100% renewable electricity, according to the company.
“We developed a glass that truly does have a lower carbon footprint,” says Stephen Weidner, president and head of Architectural Glass North America & Solar Products at NSG Pilkington. “We’ve changed the chemistry of the glass itself. The glass does have a lower carbon footprint.”
While NSG succeeded in proof of concept for Mirai, the access to fuel and supply chains don’t yet exist to allow for continuous production. “The logistics and supply chains are being developed, but it’s going to take several years,” says Weidner. “We wanted to prove to ourselves that the technology does exist for lower carbon glass.”
Turkey-based float glass manufacturer Sisecam is also aiming for carbon neutrality by 2050. To meet its goals, officials announced at glasstec its Plant of the Future platform to bring together glass producers to discover step change solutions in production. Sisecam’s Elverici says of the platform: “Plant of the Future will not only transform Sisecam’s production operations and processes but also offer significant opportunities for advancing the industry. … As we progress toward our goals of operational excellence, optimization, digitalization and sustainability, this platform will generate practical, well-designed and innovative solutions. In doing so, it will create an ecosystem where we envision together, design together, implement together, operate together and in return grow together, paving the way for collective development with all of our stakeholders.”
Manufacturers say they are accelerating investments in float production efficiencies. Saint-Gobain officials report the company has reduced carbon emissions by 4,000 tons since 2021 by boosting oxygen in the float process, waste heat recovery, renewable energy and optimizing furnace design. The company achieved a “20% improvement in energy performance with each refurbishment and a 5% reduction in energy required to melt one ton of glass from 2017 to 2023,” according to officials during glasstec. The company is also exploring alternative melting technologies, such as a 30% hydrogen-fire glass melting, being tested at a plant in Germany.
Vitro Architectural Glass has targeted carbon reduction and lower GWP through more efficient use of batch material, furnace efficiency and design improvements, energy-efficient lighting and regulating equipment, and supplier improvements, according to officials. The company also continues to look to oxy-fuel furnace technology, which melts glass raw materials mixing pure oxygen (instead of air) with natural gas, significantly improving energy and environmental performance. “This technology reduces energy consumption in glass-melting furnaces by as much as 20% and greenhouse gas emissions by 50%,” per company statements.
Glass Magazine spoke with American-based glass manufacturer and fabricator Cardinal Glass Industries, which is also investing in plant improvements to reduce embodied carbon. “Cardinal is actively pursuing new technologies that will allow us to have one of the lowest carbon glasses manufactured today. Currently, our legacy float plants have all achieved minor source of emissions status. In addition, we will have the three float lines purchased in 2021 become minor source status by 2027,” says Bowie Neumayer, vice president of sales and marketing.
Guardian Glass also introduced a low-carbon glass, Nexa, following a research and development project at the company’s Bertrange, Luxembourg, plant. The manufacturing process maximizes cullet from internal and external sources, helping to reduce embodied carbon by 30%, according to Guardian statements.
Additionally, the company released new EPDs in 2024 for glass produced in the United States, demonstrating the effect of decarbonization improvements in recent years. According to the new data, Guardian’s domestically produced glass offers a 23% reduction in GWP from the NGA’s 2019 EPD value and 24% lower than the company’s 2018 EPD. Driving such improvements in the U.S. is, in part, the Low Embodied Carbon Material Standard from the General Services Administration, which sets a performance threshold for materials, calling for products that are in the top 20% of GWP performance, according to EPD data.
While manufacturers are looking to take bigger steps to decarbonize, many small improvements at the manufacturing level also make an impact, says Alan Kinder, Guardian’s director of the commercial segment. “You don’t always have to wait for a massive cold tank repair to make changes. At our Kingsburg, California, plant we implemented a sleep mode on our coater, as it takes a lot of energy to turn it on and off. Now there is less energy required to fire it back up,” he says. “That saved the equivalent of 1,000 kilowatt light bulbs a year. By itself, it’s not revolutionizing the market. But when you implement it over 25 different float plants, and have 100 smaller initiatives at each, it makes a difference. Rain drops make puddles when we start to talk about those trends.”
Reuse + Recycling
Carbon emissions from glass can be greatly reduced when glass is recycled, beginning in the production process. Melting cullet in a furnace requires significantly less energy than melting raw materials, so the more cullet manufacturers can incorporate into the float melting process, the lower the energy costs.
Float manufacturers have long used cullet from their internal processes in melting furnaces. Glass that comes off the line that doesn’t go out to customers is made into cullet and pulled back into the process. According to Glass for Europe estimates, 75% to 80% of cullet used in glass manufacturing in Europe comes from such internal processes. The challenge for glassmakers is increasing cullet from other sources—offcuts from customers and from end-of-life glass products, according to glassmakers.
Saint-Gobain is taking on this challenge at its Aniche, France, location through the introduction of a cullet sorting process. The plant has targeted a goal of using 50% cullet in the furnace infeed for a reduction in carbon emissions of more than 6,000 metric tons per year. Achieving the goal requires not only using all cullet from internal production but also incorporating cullet from customer offcuts and from already fabricated products, either in fabrication facilities or end-use products from an existing building.
Sourcing clean cullet from existing products proves most challenging for the float process as it must be pure to ensure consistent, high-quality glass production. It requires developing new processes for manufacturers and their fabricator customers, and, down the line, potentially building contractors and recyclers. It also calls for new equipment. For Saint-Gobain, “the cullet sorting project involves investing in a cullet sorting and control line to remove impurities that otherwise make it unsuitable for flat glass production,” according to company reports.
During glasstec, machine supplier Hegla showed a technology for deconstructing IGUs so the glass can be recycled back into flat glass rather than being downcycled or sent to landfill. “Our development work was based on the question of how it is possible to deal with imperfect panes and use glass in a way that conserves resources and is efficient at the same time,” says Heinrich Ostendarp, managing director of Hegla, in a company announcement. The machine, IG2Pieces, automatically separates IGUs and enables the panes to be reused. Fabricators can use it in their own facilities, to separate rejected units for reprocessing, or the machine could be employed for high-quality, end-of-life products.
Ostendarp says he expects demand to increase for recycling and reuse of existing glass lites, as the market targets lower CO2 emissions and reduced costs. “In the future, I can imagine that new interest groups will examine the issue. In some cases, IGUs will then be separated directly on the construction site. Suppliers and buyers will come together via software platforms. I also envision new glass products, including IGUs made from fully recyclable panes. In terms of energy prices, melting will become more attractive. The demand for type-specific shards for the float tank is already high today.”
Reducing Operational Carbon
In 2024, VIG began to dominate the conversation about highest-level performing glass products. “VIG is what IG was to monolithic,” says Guardian’s Kinder. “VIG is the next evolution in glass.”
Several glass manufacturers announced new investments in the segment, including Guardian. In March 2024, Guardian and VELUX Group announced a joint development agreement for the manufacture of tempered VIG. “We’re not waiting for the market to be ready,” says Kinder, noting that higher costs and production limitations continue to be a hinderance for widespread adoption. “There is a strong belief at the Department of Energy level that VIG is the future. … We’re engaging right now. We’re asking, ‘what do we need to do to be impactful in that business?’”
Meanwhile, Vitro announced its VacuMax VIG that offers “wall-like R-values up to R-20,” according to company officials. Additionally, the company is working to bring VIG manufacturing to North America. “We need America-based manufacturing,” says Vitro’s Fernando Diez, global vice president of marketing. “VacuMax is currently manufactured overseas, and if we want to go massive with it, domestic manufacturing is key.”
NSG Group has been at the forefront of VIG, producing the Spacia product for more than 30 years. “We have quietly installed in the U.S. dozens and dozens of buildings reglazed with Spacia,” says Weidner, with much of it going to reglazing of projects—replacing old monolithic lites with high-performance VIG. “This dramatically improves the existing façade, just by changing the glass,” he says.
Additionally, the U.S. has seen the emergence of LuxWall as a domestic producer of VIG. In October 2024, the company announced it raised $51 million in funding to scale up production at its newly opened factory in Litchfield, Michigan. The money will also go to the construction and expansion of a second factory in Detroit and a research and development facility in Ypsilanti.
“With 50% of building stock still single-pane windows, and 25% of the energy used to heat and cool them lost through windows, the market opportunity for LuxWall is massive, and LuxWall technology is primed to help significantly reduce carbon emissions from the built environment,” says Cindi Bough, managing director at the venture capital firm Climate Investment.
Looking ahead, Saint-Gobain also plans to commercially launch a new VIG line in 2025. During glasstec, the company announced its VIG line INSIO, which stands for insulation, innovation and optimization. The company showed the first prototypes of its new range of vacuum insulating glazing and hybrid VIG.
At Cardinal, “we are evaluating various VIG technologies and how they may fit in the residential industry,” says Neumayer. “They do offer the next step in thermal performance, but at the same time, have variability in materials, aesthetics, durability, cost and availability.”
Solar Demand on the Rise
The solar panel manufacturing market has continued its healthy growth since the passage of the Inflation Reduction Act in 2022 incentivized both the production and purchase of clean energy equipment. Solar panels, also called photovoltaic panels, use glass, and both NSG Group and Vitro Architectural Glass have supply agreements with First Solar, a solar panel manufacturer.
Canadian Premium Sand also plans to open a patterned glass facility in Selkirk, Manitoba, Canada, to supply solar panel manufacturing, and announced in November 2024 that the company is also pursuing plans to open a patterned glass facility in the U.S., repurposing a former glass manufacturing facility to produce 4 gigawatts per year of solar glass. The company has established CPS Glass USA Corp., a wholly owned U.S. facility, as part of this new venture.
Anshul Vishal, vice president, corporate development, says their customers have a few interests regarding glass production, other than supply. Some customers have started asking for thicker glass, due to the increasing intensity of hail in certain regions of North America. “What we’re hearing is a lot of solar projects are having difficulty with expensive insurance policies and that’s to do with hail damage and the cost of replacing glass,” says Vishal.
Manufacturers are also concerned with the supply chain of materials. One reason is that the IRA incentivizes use of domestic materials over overseas imports, says Vishal. Another reason is increased regulatory interest in “the carbon footprint of the products and traceability of the supply chain going up a few levels,” he says. “As all of the new facilities that have been announced for solar panel manufacturing come online in the next year, we suspect there will be a lot more scrutiny on the supply chain.”
Vishal doubts that the North American glass industry will be able to supply this new sector due to capacity. CPS Glass by itself will be able to supply, at most, 20% market share, he says; part of the barrier remains the cost of glass manufacturing in North America. When the solar panel market reaches 80 GW in capacity, Vishal says this would require billions in investment in glass manufacturing to supply the industry. “I think there’s always going to be imports coming in, just because of the size of the market,” he says.