Don’t forget the frame
Thermal barriers open opportunities for buildings’ energy efficiency
Buffalo Public School’s modernized Houghton Academy in New York using Wausau Window and Wall Systems’ high-performance windows with Technoform’s extra-wide polyamide thermal barriers. Photos by Orchard Photography.
Today’s commercial curtain wall, storefront and other fenestration systems can help protect us from extreme temperatures and conserve natural resources. While high-performance glass often is the first component we see, it’s essential to remember the role of the frame itself.
Aluminum has consistently proven to be the material of choice for fenestration framing because it is strong, corrosion resistant, fabrication friendly, long-lasting, infinitely recyclable and can be finished in an almost unlimited choice of colors. It also is a good conductor of thermal energy.
Without a physical thermal barrier to separate the aluminum framing’s exterior and interior surfaces, energy will “bridge” through it. This causes heat loss from the interior when it’s cooler outside or heat gain when exterior temperatures are warmer.
How to make a system thermally broken
Whether your building is in a warm or cold climate, the goal for thermal improvement is the same: minimize heat transfer.
“Thermally broken” fenestration systems interrupt the energy transmission by creating a cavity in the aluminum framing members and inserting an insulating barrier to reduce thermal bridging. There are two main methods for accomplishing this: polyurethane pour-and-debridge (P&D) or polyamide thermal strut.
P&D
With P&D, you remove aluminum from a solid extrusion to form the cavity. The two-part polyurethane is poured into the channel. After it cures, the metal bridge from the bottom of the channel is removed, or “de-bridged.”
Thermal strut
With thermal strut, you begin with two separate extrusions. These define the cavity and are joined with the polyamide strut to become the exterior and interior framing. This method also offers an economical option for “two-tone” dual finishes.
Both methods offer improved thermal performance and potential energy-saving benefits for all aluminum-framed fenestration applications―from mid-rise schools to high-rise offices. Manufacturers also can widen and add cavities with thermal barriers for increased performance.
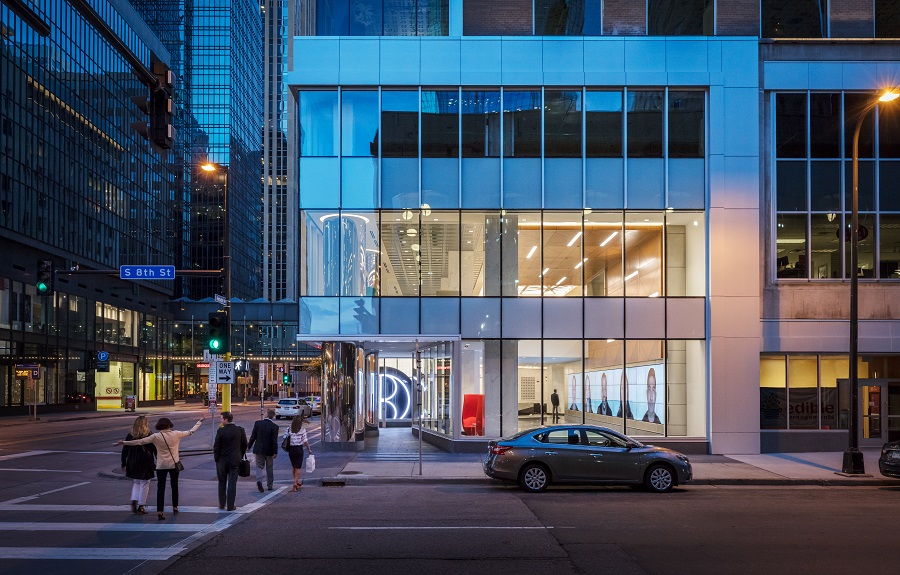
The Baker Center renovated, mixed-use, office building in downtown Minneapolis features Tubelite’s thermally broken curtainwall and storefront. Linetec incorporated both Technoform’s thermal strut and Azon’s P&D thermal barriers within the aluminum framing and finished it with clear anodize. Photo by Paul Crosby.
What can thermally broken framing do?
Thermally broken framing and increased daylight help building occupants to reduce their use of electric lighting and reduce demands on the HVAC. Further reducing HVAC usage, operable windows and sliding or terrace doors also provide a seasonal opportunity for natural, passive ventilation. Products and behaviors that minimize energy consumption typically contribute to lower utility costs, as well as lower emissions that benefit our communities.
Thermal barriers also enhance fenestration systems’ condensation resistance. Without intervention, the moisture from condensation can damage adjacent materials and promote mold growth. Avoiding mold and mildew improves indoor air quality, supports healthier interior environments and extends the building materials’ lifespan.
How to select a supplier
Manufacturers can save time, labor and hassle when choosing a single-source provider that can offer both P&D and thermal strut choices along with finishing, stretch forming and other services in one location. Not only will your products be warrantied to meet their specified requirements, you also can be confident that their high-quality, finished aluminum will look and perform their best for many years to come.