Check the spec to ensure anodize finishes deliver durability
Anodize offers performance that other coatings may not
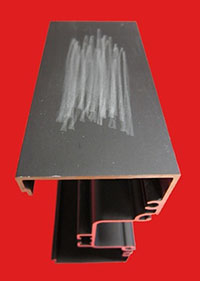
Traditional dark bronze anodize aggressively rubbed with a nickel
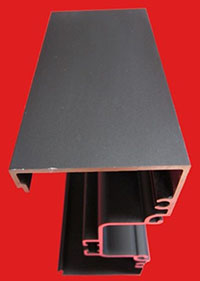
Traditional dark bronze anodize wiped with wet towel after a nickel rub
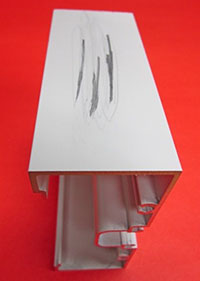
“White anodize” aggressively rubbed with a nickel
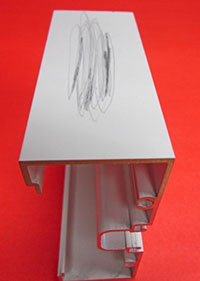
“White anodize”
wiped with wet towel after a nickel rub
For aluminum building materials and surfaces, anodize provides one of the most durable and longest lasting finishes. But remember to check the specification to ensure it will deliver the intended, required result.
How anodize performs on buildings
Anodize finishes are created through an electro-chemical process where the aluminum on the surface of a part is converted from aluminum to aluminum oxide, an extremely hard and durable surface finish. Aluminum oxide is second only to a diamond in its hardness. Due to these properties, and because the coating is integral to the metal part itself, anodize is highly resistant to marring, scratching and other damage often associated with the needs of high-traffic environments.
A fun and easy way to demonstrate the durability of true anodize is to take an ordinary nickel coin and rub it back and forth across the anodize aluminum. It looks like the coin is scratching the surface, but in in fact, it is the nickel that wears down against the hard anodized finish.
Understand the specification
When selecting and specifying anodize finishes, it is important to understand what is truly being offered. For architectural aluminum products’ finishes, there are two primary specifications:
- AAMA 611-20, Voluntary Specification for Anodized Architectural Aluminum, which details Class I, a high-performance, durable finish used for exterior building products, and Class II, a lower performance, less-durable finish recommended for interior applications,
- AAMA 612-20, Voluntary Specification, Performance Requirements, and Test Procedures for Combined Coatings of Anodic Oxide and Transparent Organic Coatings on Architectural Aluminum.
Both are standards of the Fenestration and Glazing Industry Alliance (FGIA) and each addresses aluminum finishes, but there are several key differences. In AAMA 611 the only coating called for is an anodic coating, while AAMA 612 calls for a very thin anodic finish with an organic coating (paint) applied over the top of the anodic coating.
“White Anodize” can compromise product hardness and performance
One finish offered with the 612 specification is referred to as “white anodize.” The white color is achieved by applying a thin, organic coating over the aluminum’s minimal, integral anodic finish. Unfortunately when paint covers the aluminum oxide, the extreme hardness and wear properties of the anodize are compromised.
As a result, the coatings specified in AAMA 612 do not have nearly the surface hardness, performance benefits and durability of traditional anodize coatings. Similarly, they also do not have the weatherability, color-fastness and the longer warranties associated with high-performance PVDF architectural coatings that meet AAMA 2605.
If durability is the priority in selecting a finish for architectural aluminum, coatings that only meet the AAMA 612 specification will not suffice. For the most durable and wear-resistant finish available, choose anodize specified to meet AAMA 611 Class I.