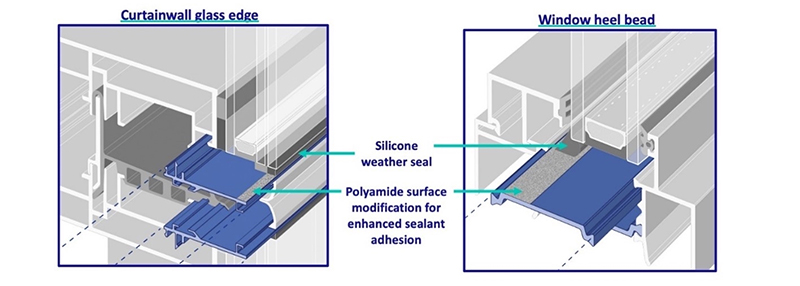
Polymer thermal barrier technology’s use in aluminum fenestration to increase thermal performance is growing, driven by increasing code stringency and market demands. As designs integrate wider and more complex thermal barriers, there’s an increasing need to bond sealants to these polymers - not only to support weatherproofing, but also to meet structural performance requirements.
Consider a window’s silicone heel bead, which bridges the joint between the glass and the sash or frame. Now, it may need to adhere to the polyamide rather than aluminum to create a window’s water barrier. In curtain wall, where the aluminum glass edge piece is replaced by a polyamide profile to enhance thermal performance, the exterior silicone weather seal needs to maintain the same reliable adhesion to the polymer surface.
The adhesion of sealants to polymers is typically not as good as to aluminum, and primers are often needed to support adequate adhesion. To enable more thermally advanced aluminum fenestration solutions, it’s therefore important to address this adhesion challenge.
New technology creates opportunities for adhesion
A newly available technology modifies the thermal barrier's surface to provide the same level of adhesion to sealants as provided by finished aluminum and without the need for surface primers.
The surface modification creates a layer of aluminum oxide (alumina) particles embedded in the polyamide’s surface. This new surface forms a solid alumina interlayer between the polymer and sealant, which has the same highly reliable adhesion to silicone as finished aluminum extrusions. Note that the surface of anodized aluminum is also alumina, which is known for excellent sealant adhesion.
Consider the new surface layer as a “micro-aluminum profile” bonded to the surface of the polyamide. But, since the aluminum oxide surface is non-continuous, its presence does not degrade the thermal properties of the polymer barrier and the polyamide remains fully recyclable.
Creating more opportunities for use of polyamide thermal barriers
The bond created between this modified polyamide surface and silicone is strong enough to meet all the structural requirements of ASTM C1401 – Standard Guide for Structural Glazing Sealants as a substrate for silicone adhesion. Excellent silicone adhesion has been shown after 5,000 hours of UV exposure and after 196 hours of aggressive salt-fog (marine) conditions, with no bond degradation between the embedded alumina and polyamide or between the coated polyamide and silicone.
This new adhesion technology delivers additional freedom for using polyamide thermal barriers even more widely in fenestration system design, particularly in areas where structural adhesion is critical.