Swisspacer Air Provides Pressure-equalized IG for Denver’s Humboldt Project
The “Humboldt Project” was recently completed in the Whittier neighborhood of Denver. The modern residential complex of three single-family homes mainly inspires with its cubic architecture and large windows. Not least because of the enormous differences in height along the transport route from the production site in Poland to the installation location, the triple glazing units were fitted with the innovative Swisspacer Air, an intelligent solution for pressure-equalized insulating glass.
Designed by the local architecture office Studio Limited, the three residential buildings of the “Humboldt Project” harmoniously integrated into the existing development, combine trendsetting building design with consistent sustainability. The two-story buildings are noted for their clear, purist design, a high proportion of transparent surfaces, lots of daylight and openness in the room design, as well as the use of high-quality materials.
Aesthetic architecture and energy efficiency
On the search for an optimal solution for the 48 windows and sliding doors, some of which are quite large, the architects relied on the expertise of Vonderhaus, a provider of high-performance window systems in North America.
To meet the high demands for the design and energy efficiency of the “Humboldt Project” the experts from Vonderhaus constructed the windows using modern triple glazing units with warm edge spacer bars from Swisspacer, produced in Europe by the Polish glass specialist Vitroterm.
Matthew VonderHaar, managing director at Vonderhaus, says, “For new buildings in Denver, the locally applicable standard IECC 2018 requires a maximum U-value of 1.70 W for windows. With the selected glazing and the thermal break in the glazing edge, we were able to meet the requirements without any problem and achieve a U-value of 0.9 W.”
Reduced risk of breakage
Another special challenge on this project was the long transport route with enormous differences in height of almost 4,600 feet between the Polish production site and the installation location in Denver.
Matthew VonderHaar: “For projects situated more than [3,200 feet] above sea level, we only use the Swisspacer Air. It is the best option for reducing the hazards that can be caused by the difference in pressure. And we can be completely relaxed in case of last-minute changes to the transport route.”
The Swisspacer Air is a metal sleeve with integrated special membrane, and is integrated directly into the spacer bar. The special structure brings about a permanent, slow equalization of pressure between the surrounding environment and the cavity between the panes. This enabled safe transport, even given the extreme conditions.
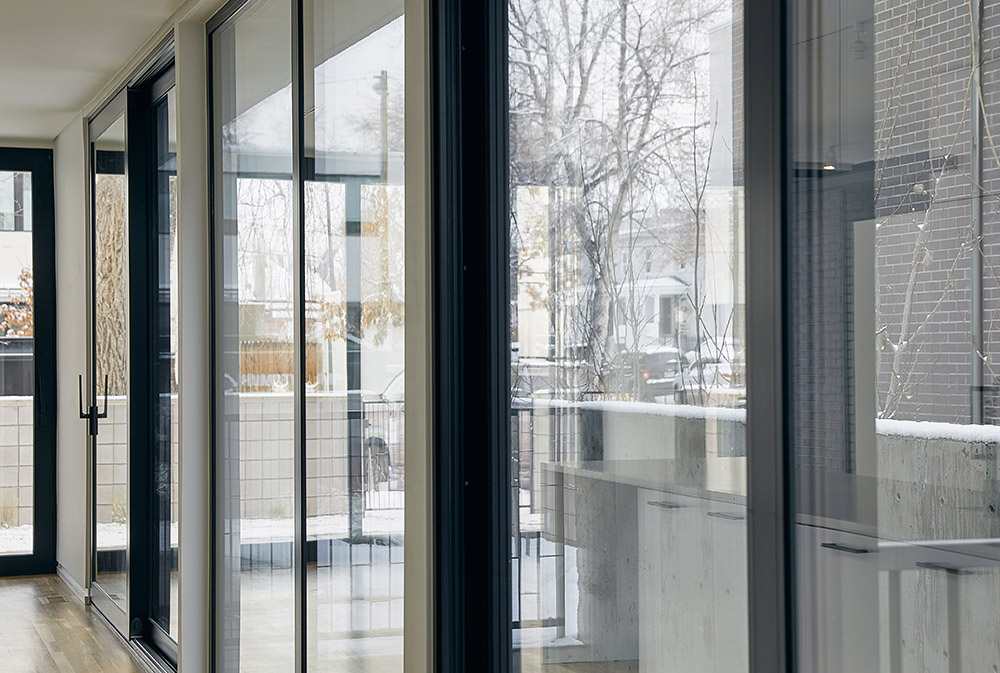
In the case in question, the insulating glass units were transported by freight ship, train and truck, and with many differences in temperature and height. Matthew VonderHaar: “We use Swisspacer Air because of the good experiences we have had on all projects constructed at heights over [3,200 feet]. Unlike common height measuring systems, the component reacts to each and every load that can occur during unplanned deviations from the chosen route. It adapts constantly to the air pressure in the immediate environment and constantly regulates the pressure in the cavity between the panes. In our opinion, it is far superior to the capillary systems previously used.” Ultimately, using the Swisspacer Air enables a larger cavity between the panes, which also improves sound insulation.
Simple, manual installation
The Swisspacer Air was very simply installed in the glazing edge of the insulating glass units produced at the factory of the Vonderhaus’s long-standing partner Vitroterm in Poland. Once drilled, the component was screwed into the Swisspacer Ultimate warm edge spacer bar. For insulating glazing units that are delivered to the U.S. and Canada, Vitroterm and Vonderhaus have long used this intelligent solution as standard, thereby ensuring greater transport safety and a minimised risk of breakage.