A How-To Guide to Routine Maintenance
Why it's importance, and simple steps to achieve it
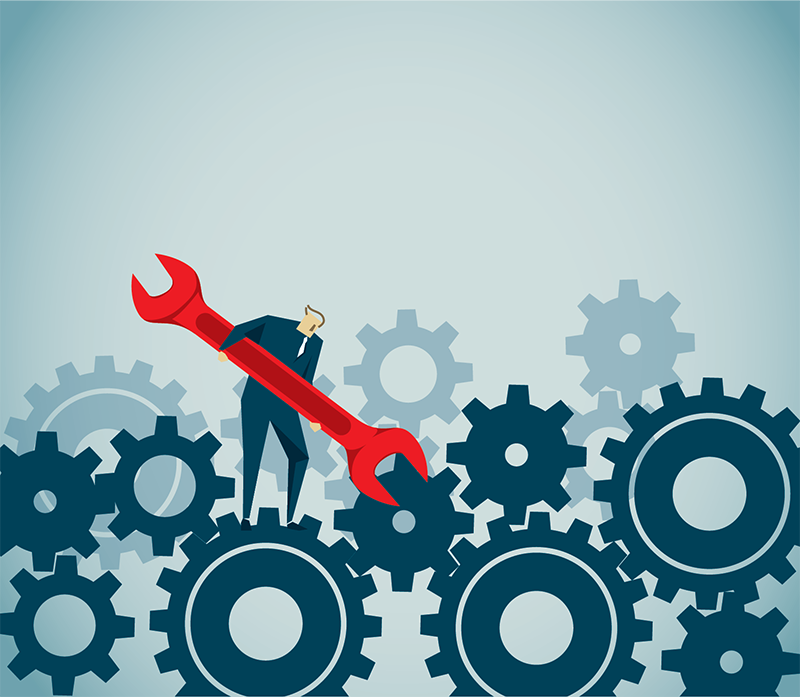
We firmly believe providing high-quality equipment, products and support is the best way we ensure the quality our partners’ produce. We stand behind our products so you can stand confidently behind yours. However, supplying the equipment, tools and support is only the start.
A complete production process is a well-oiled machine requiring all parts to work together to perform at maximum efficiency. When it comes to the longevity and efficiency of your equipment, routine maintenance is vital. Regularly scheduled maintenance not only ensures your items are functioning properly but also helps to identify potential issues before they become major problems.
So, let me provide you with some easy steps to keep the equipment you rely on performing at its best. Following these can ensure that your equipment is properly maintained, can help you avoid expensive repairs, and will help ensure you’re giving your partners the quality they deserve.
Why Is Routine Maintenance Important?
Saves Money
The old saying is penny wise and pound foolish. By performing routine maintenance, you can identify small issues before they turn into larger, more costly problems. In the long run, regular maintenance will save you money by avoiding expensive repairs and replacements.
Increases Lifespan
Regular maintenance without a doubt extends the life of your equipment. A well-maintained item will perform better and last longer than one that has been overlooked. A grinding spindle with years of glass build-up must work harder than a clean spindle. Electric motors these days are not inexpensive, and if they’re working harder that means a shorter lifespan.
Improves Efficiency
Clean spindles allow your equipment to run at optimal speeds, as does a proper coolant to water ratio. Not replacing brushes leads to scratches and remakes. Not properly indexing diamond wheels means cutting too much or too little off your glass and/or poor polishing.
Ensures Safety
Timely maintenance will catch a safety hazard before an incident. Glass processing requires water and electricity, you want to make sure water is staying where it is supposed to be, and not being exposed to electrical current.
Steps to Follow for Routine Maintenance
Create a Schedule
This is number one on the list for a reason. Most, if not all, equipment manufacturers have the maintenance schedule in their manuals. It will tell you what to do and when to do it.
The daily/weekly items should become part of the routine for daily operation. For longer-term items, create an automatic calendar in Outlook to generate reminders before they’re required. As these are often more in depth, the heads up will allow you time to plan to take the machine out of service, if needed, to complete the maintenance.
Daily maintenance tasks should be printed, laminated, and then displayed on the equipment itself. You can go further and create checklists for each interval which confirm what was done, when it was done and by whom. This holds everyone accountable for keeping your equipment in the best condition.
Cleaning
This should be part of the daily schedule, listed separately to stress importance. Glass grindings are like cement; if you let them build up it takes so much more time to remove. Those hard grindings reduce the machine’s efficiency as stated above.
Ask one of our field engineers what most of their time is spent on when on a job, and they will tell you without a doubt it is cleaning.
Hire a Professional
Use the experts for what they’re best at; yes, they can clean, but so can your team, who need not know the full ins and outs of a product.
Even when you’re maintaining your equipment properly, there are advantages to bringing in the experts. For the large or intricate jobs, they’ll ensure the job is done correctly and safely. Preventative maintenance contracts are supplied by most all equipment providers, so take advantage of them. They are designed for you and the manufacturer, allowing you both to catch a (metaphorical) spark before it turns into a raging fire. If we’re at your plant checking equipment twice per year, we hold some responsibility for your equipment performing properly.
Replace & Stock Spare Parts
Glass is a hard material and processing glass wears everything. This makes it critical to replace items when they should be replaced. The best companies replace items before they are worn out because they know if they wear completely it is going to start wearing other items and creating a larger expense.
Your equipment provider should have a suggested parts list to keep on hand; these are items which, if they go out, are going to prevent the machine from operating. Having these spares on hand allows your equipment to get back online quickly, and without adding extra costs of next day shipping a motor that weighs hundreds of pounds, or scheduling an emergency service visit that may take a week or two to get.
Communicate across the team
Open communication between operators, supervisors, management, and maintenance teams (if you have them) is highly valuable. Explain to all what is going to be done and why it is important. Create an environment where the team is proud of the equipment they’re responsible for.
When they see it as their own, they will want to keep it in the best shape. Management should support and communicate with those they rely on to produce the quality that is expected of them. You do not want an environment where there is fear of mentioning something is broken or needs to be replaced.
Now you see why routine maintenance is essential for the longevity, safety, and efficiency of your equipment.