Strategic Automation & Software Solutions
4 ways to efficiently automate production
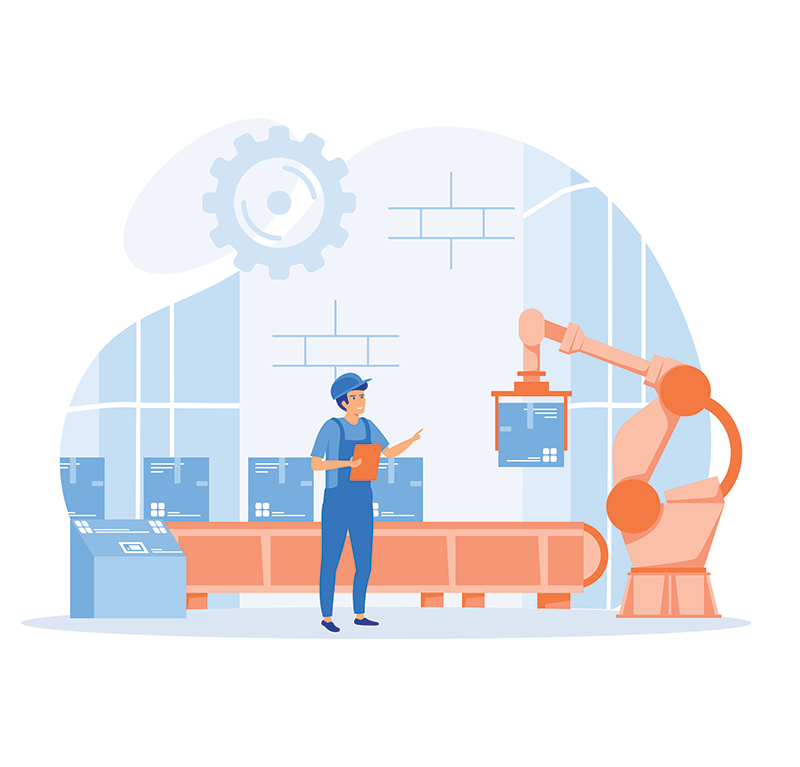
My previous blog referred to challenges and limitations of automating custom glass manufacturing with robotic solutions, and I stressed the critical role of human expertise in manufacturing. However, strategic automation, particularly through software solutions, presents a promising avenue for enhancing efficiency. With the right balance between automated solutions and skilled human labor, glass fabricating plants will achieve greater productivity and long-term sustainability.
I want to explore areas in glass fabrication where other automation can be effective. These include Enterprise Resource Planning systems, cutting optimization, quality control and material handling. By automating these solutions, companies can retain more people. Automated solutions for these processes allow companies to improve efficiency and keep employees by moving them to other processes that require more manual input, all while maximizing efficiency.
Integrated ERP Systems for Enhanced Efficiency
A foundational step in automating a custom glass fabrication is an ERP system which allows employees to follow product throughout the plant in real time. A proper system plans the most efficient route for your product to flow through the plant. Something as simple as a barcode scanner at each step of the fabrication process can provide enormous gains in efficiency as it allows for easier tracking.
Furthermore, ERP systems are typically equipped with modules for importation of the data into your specific fabrication centers, like the cutting cell, CNC fabricating, tempering, all the way to packaging and shipping. Data is seamlessly transferred from a client’s approved drawing to your vertical CNC machine for precise milling and drilling to the exact specification. This kind of automation reduces human error and increases throughput, allowing skilled labor to focus on other value-added tasks.
Cutting and Optimization solutions
In most glass fabricating plants, the cutting line is the heart of the operation. It feeds the entire facility; inefficiency here is felt exponentially throughout the plant. Therefore, this is one of the most critical locations to automate, even with a bare minimum cutting optimization software.
Cutting optimization streamlines your process, ensuring materials are used with maximum efficiency, reducing waste and speeding up production. By automating the optimization of cutting patterns, manufacturers not only save on material costs but also expedite the production cycle drastically. Using optimization software with a full ERP system allows manufacturers to label each cut piece with all the information specific to that piece of glass. This improves production flow, as barcoded labels allow product to be scanned in and out of each following processes; if a piece of glass gets damaged the ERP puts it back in line for remake, preventing further cost of production. Benefits of this automated process include traceability and fewer errors.
The cutting department is a location in the plant that can easily integrate higher automated equipment solutions, including robotics. After all, most glass comes in a large, standard, rectangular sheet size where we use a repetitive process of cutting down large lites to smaller, manageable sizes for further processing needs. Automatic loaders, glass shuttle and retrieval systems pair seamlessly with your cutting table and are proven to do more with less human capital. Automated solutions also provide a safer environment for one of the more dangerous parts of a custom glass fabrication facility.
Automated Quality Control Systems
Automated visual inspection systems can identify defects early in the production process, even as early as the first cutting process. These systems use high-resolution cameras and advanced image processing algorithms to detect imperfections that might be overlooked by the human eye. They’re so sophisticated they can measure tempering bow as the glass is coming off a tempering oven and instantly approve or reject the glass.
Skilled labor can address specific issues, enhancing the overall product quality. Remember, anything rejected before it gets out the door is a savings. You’re not wasting time and resources further processing glass that is going to get returned. Automating as much of the QC process as able is tremendously valuable.
Again, pairing QC automation with ERP is a win-win. Once an item is rejected, the system instantly sends a remake piece to the front of the cutting queue with a new, hot label, alerting all processes downstream that this is an important piece and designating where it needs to go.
Material Handling and Logistics
As previously discussed, the cutting cell is an excellent location for automation, and so is each individual processing station which use things like glass manipulators and lifters. They’re not only safer, but they also allow an operator to do more with less. The heavy glass that normally takes two people to run on a vertical edger can be run with one person using a lifter and an overhead system.
In the future, I think we’ll see more automated carts, and automated transport within plants. It is only a matter of time before technology like Amazon and large warehousing facilities that have been using it for years is brought to our industry. Once a cart is strapped and ready, a battery-operated cart takes it from the fab center over to the tempering line. Glass is heavy, and no one will mind that at the push of a button their cart goes to the next stop.
By carefully selecting areas for automation, glass production facilities can improve efficiency and maintain agility while leveraging the unique skills of their workforce. Strategic automation allows for a reduction of human error and the optimization of resources, which are vital in a competitive market like we find today. This approach not only respects your invaluable human resources but also positions companies for future growth and innovation.