Why Robotics Aren't a One-Size-Fits-All Solution
Exploring the future of flat glass fabricating equipment
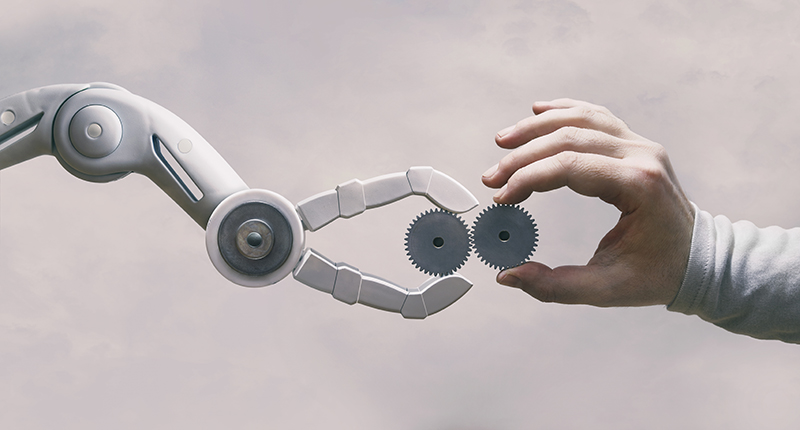
The fire suit is on. I am going against our largest industry trend, automation. Automation, after all, is being pushed as THE answer to problems large or small in all industries, right along with AI. While these are powerful tools, utilizing them in the incorrect way will set you behind.
The train took off years ago and is barreling towards full speed. Feeling like an unstoppable beast, no longer a trend and yet we’re still not preaching robotics are the answers to all your challenges. Why??
My 0.02 cents: what robotics can, and can’t, do
Would be easy for our company to jump on the “Robotic arms are THE answer!!!” train. We can offer robotic arm solutions, many ask about them, they come with higher prices and greater revenue opportunities for our company…but there is a problem.
When it comes to glass fabricating equipment, part of what we do here, a robotic solution is being pushed as a silver bullet. But, the often highly customized nature of glass fabrication presents unique challenges robots struggle to overcome, leaving users with a solution that feels great and says “I’m cutting edge,” but a traditional piece of equipment can do it just as well, and often better, at lower cost.
Robotic solutions struggle with variety
I have seen many varying robotics solutions in real-world operation and what I see most is batch processing, usually with a person or two watching the line. Commonly, they are processing perfectly square glass, something a double edger line is ideal for. Some are handling slightly out of square glass, but if it is too out of the norm, the line won’t accept it or it causes an issue, stopping production.
The most impressive vertical systems that do it all—edging, drilling, milling, washing, etc. —are slow and the edge quality isn’t that of traditional vertical edgers. It’s impressive to watch it do it all in one run, however splitting this work into traditional vertical edgers and independent CNCs (which you can feed directly from a vertical edging line) can give better quality, greater capacity, greater flexibility, and lower risk if one part of the line malfunctions. Additionally, this setup requires a lower initial investment than a robotic solution.
None of the robotic solutions for vertical edgers I’ve seen were running an uninterrupted, non-stop flow of product in varying sizes, out of square, and varying thicknesses all in succession. Automated solutions do exist that accomplish that kind of processing, but it doesn’t have an attractive, multi-axis arm moving glass from one place to another.
Elon Musk and using robotics at Tesla
Here’s a real-world example I learned about from reading Walter Isaacson’s biography of Elon Musk:
Tesla’s plant in Fremont, California, faced the challenge of meeting ambitious capacity requirements. The plant was shooting to produce something like 3,000 vehicles per week; without delivering this quantity within this time frame the company was likely going to fail. Setting up the facility they thought, like most, they should have as much automation as possible, with robots everywhere they could. Robots never get tired, they do not take breaks, and they’re supposed to be faster.
Yet Telsa was stuck at something around 2,000 units, far short of what they had to do to survive and were looking doomed to fail. What Elon determined was that automated robotic processes were dramatically inhibiting their capacity. Robots were taking exponentially more time than a person would take to do the same task, and the robots would often fumble with the process where are person did not.
To accomplish their lofty goals, Elon found a solution was to reduce vast amounts of robotic processes they thought were getting them ahead. Solutions that likely cost them hundreds of thousands of dollars each were marked with a Scarlet A and immediately removed. They were replaced with humans who could accomplish an identical task in less time. Shortly thereafter, they met their weekly target and now far exceed it having learned from their mistake.
I do not get the impression Elon is against robots, not in the least; hell he is building one. And neither am I. Rather, I believe Elon found automation to be best implemented after an exhaustive study of where it provides true value. Certain processes will be easy, others in custom glass fabrication still require the knowledge and intuition of a person. Combined with the dexterity of a human body that can adapt instantly, after all, our human “software” changes on the fly.
Striking a balance between human software and robotics
We all agree labor is a challenge across all industries all around the world. There are other ways of solving this challenge, finding, hiring, and retaining the right people. The culture of a company goes a long way and now, more than ever, the family culture of glass fabrication is near extinction and perhaps this is part of the problem.
Our industry is pushing towards replacing people on the lower end of the pay scale with highly skilled technicians and software engineers who are paid accordingly. Robotic arms and start-to-finish fully automated solutions remain at the highest prices and as are their parts, service, and expertise.
While automation holds great promise for improving efficiency and productivity in flat glass fabrication, it is not a one-size-fits-all solution and especially insofar as processing equipment. Our unique challenges present obstacles robots struggle to overcome. Recognizing the value of people is essential in navigating the future of flat glass fabrication. By striking the right balance between automation and human involvement, fabricators can unlock new opportunities for innovation and success in this dynamic industry.